What is a Field Network?
A field network enables controllers, I/O devices, control devices, and communication devices to exchange information for seamless processing and production.
Major Applications
Hierarchy indicates network layers grouped by use purposes in the field network world, as shown in the figure below. The typical field network applications at respective layers are as follows:
Management Layer
File transfer involves exchanging data, like production results, in file format between PCs/server computers and controllers.
Controller (Device) Layer
Message communications involve sending commands between controllers on the field network for control or data exchange.
Data links establish shared areas for multiple controllers in the network, enabling data exchange.
Component Layer
Remote I/O communication involves a controller exchanging signals with remote input/output devices through field network communication.
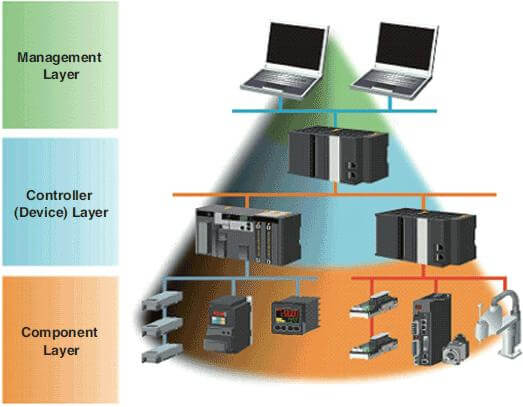
Types of Field Networks
Omron provides network products that offer the best performance for each layer
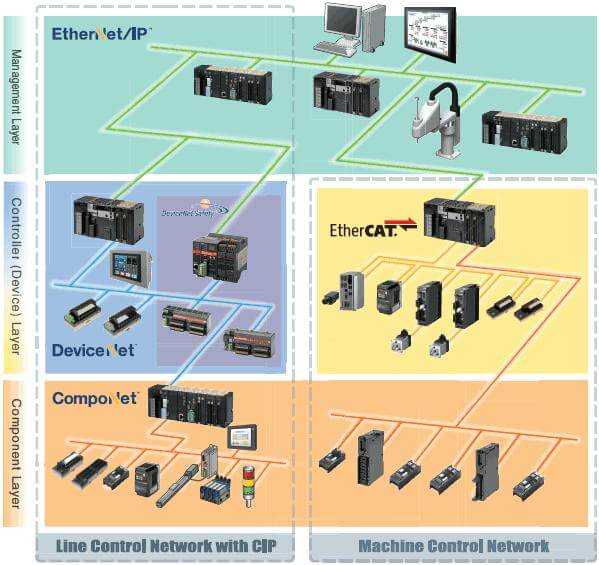
EtherNet/IP
EtherNet/IP is an industrial open network using Ethernet technology. It forms data links with specific peers, providing high-speed, efficient programming with tags.
DeviceNet
DeviceNet facilitates connection of I/O and safety components. It allows both control and safety devices on one network for optimal system performance, suitable for up to 500 m and 64 nodes. It supports various communication specifications for diverse devices and offers a multi-vendor system configuration with products from around 900 companies.
EtherCAT
This ultra-high-speed open network seamlessly integrates multi-axis synchronization and remote I/O, enabling rapid, precise control across the system.
It supports 147 axes in 0.125 ms, offers sub-microsecond jitter (<1 μs), and handles ultra-fast I/O with 1,000 points in 30 μs (for digital I/O).
CompoNet
CompoNet, situated in the sensor and actuator layer, combines high speed, capacity, and simplicity for efficient machine construction.
It features flexible branching (up to 384 nodes), high-speed communication (1 ms for 1024 I/O points), and cost-effective cabling to reduce overall system costs.
Application Examples
Remote I/O Communications
Remote I/O communications in the field network layer facilitate controller control over remote input/output devices. Controllers feature a master station, connecting signal lines to dedicated terminal blocks (remote terminals or slave stations). Certain control devices, such as temperature controllers, can integrate remote I/O communications directly. This configuration enables remote controller placement, multi-machine control, and reduces installation effort, time, and wiring space due to fewer communication lines.
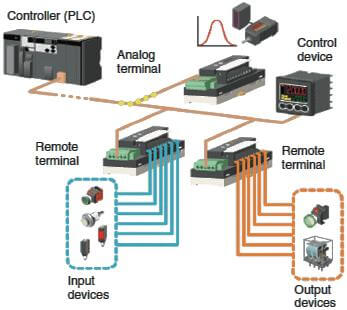
Data Link Communications
Field networks, specifically at the controller layer, facilitate data link communications among multiple controllers, enabling data sharing and mutual exchange of information like operation status. These exchanges begin automatically when the controller operates, occurring cyclically without the need for user-written communication programs. This approach eliminates the necessity for creating user programs for data exchange, leading to reduced program size.
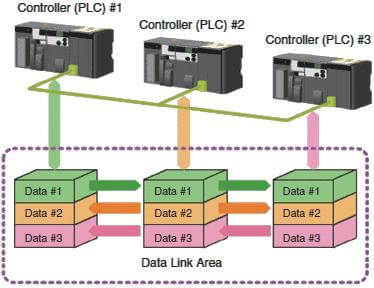
File Transfer Communications
File transfer is a common field network application at the management layer. It facilitates data exchange between PCs, servers, and controllers in file format. Received data can be utilized within user programs.
This simplifies data processing and reuse for production management software. Additionally, storing data on a server computer with mass storage disks reduces hardware costs by eliminating the need for a storage device within the controller.
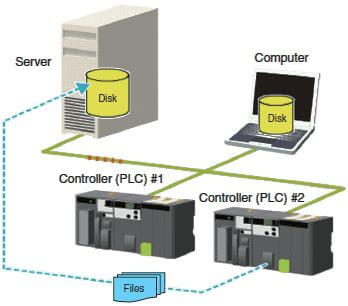
System Configuration Example
The devices composing an EtherCAT network are shown in the figure below
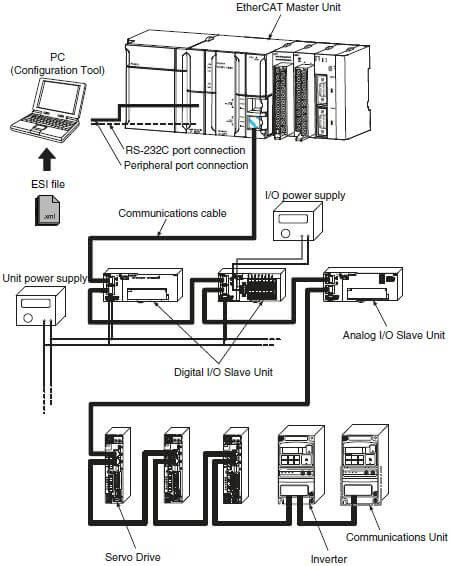
EtherCAT Master Unit
It administers the EtherCAT network, monitors Slave Units, and exchanges I/O data with them.
EtherCAT Slave Unit
It either receives data from the EtherCAT Master Unit or sends data to the EtherCAT Slave Unit via the EtherCAT network.
Two types of units are available: Digital I/O Slave Unit and Analog I/O Slave Unit.
Communications Unit
It can function as a Slave Unit within the EtherCAT network when connected to an inverter and other devices.
Configurations Tool
This PC software is used for configuring the EtherCAT network and each Slave Unit. It can function either connected to the EtherCAT Master Unit or as a standalone substitute.
Communications cable
Ethernet cables of at least Category 5 (100BASE-TX) or higher are employed, featuring double-shielding (aluminum tape and braided shielding), and they are connected directly.
ESI (EtherCAT Slave Information) file
The information for EtherCAT Slave Units is detailed in an XML format file. By importing this file into the Configuration Tool, it simplifies tasks like mapping Slave Units to I/O memory.
Unit power supply
It supplies power for Slave Unit communication and internal functions. When wiring, keep it separate from the I/O power supply.
I/O Power Supply
It supplies power for input/output operations in connected Slave Units, requiring a separate power source during wiring.
Interested to find out more about Omron Field Networks? Feel free to contact us!