Thermal Condition Monitoring for Electrical Bus Duct
Semiconductor Manufacturing Plant in Singapore | Machine making
Monitoring the temperature of the Bus Duct at Semiconductor manufacturing facilities or any power plant is vital as any loose bolts or bad welding can lead to abnormal rises in temperature and pinpoint hot spots. This problem faced by many has led to costly and expensive unexpected plant shutdowns. Bus ducts that are located overhead are often overlooked or neglected when performing electrical maintenance. Location and accessibility can make efficient bus duct maintenance a rather tricky task.
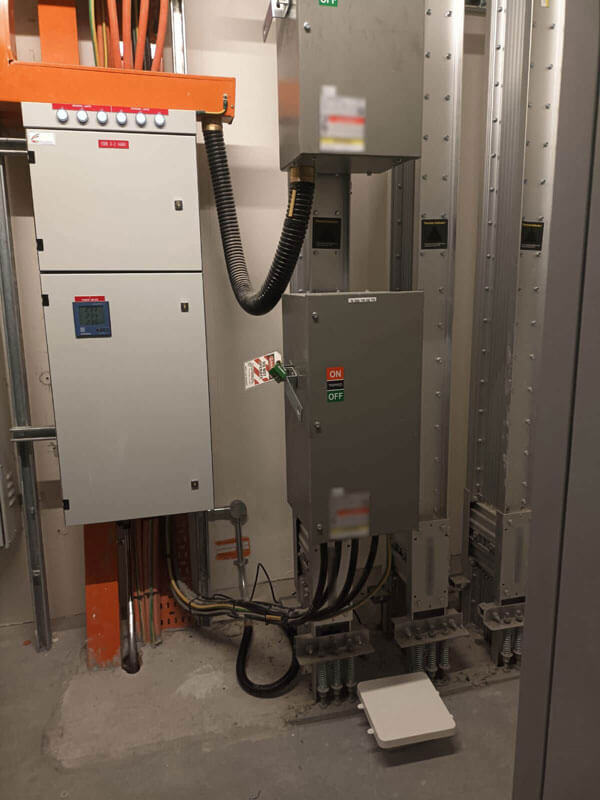
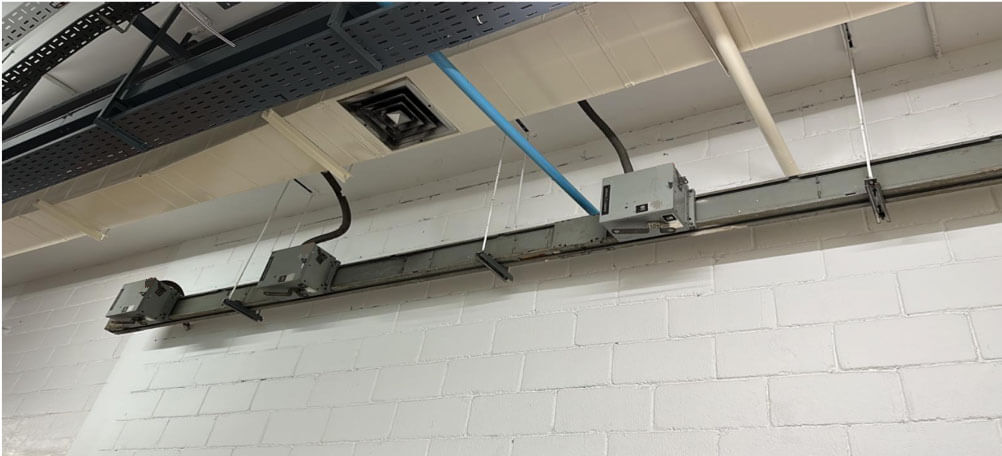
Many bus bars that are used in data centres and infrastructures are uninsulated strips of highly conductive metal that have lower electrical resistance than insulated power cables. This enables large electrical currents to be carried and thus are suitable for use in power distribution systems at many semiconductor manufacturing plants.
Flexibility, expandability and ease of maintenance of the bus duct systems are also other key attributes that eradicate existing problems faced in conventional power cable systems used in data centres and manufacturing plants which require a constant extension, re-installation and capacity modification of loads.
The Challenges
Abnormal overheating of bus bars
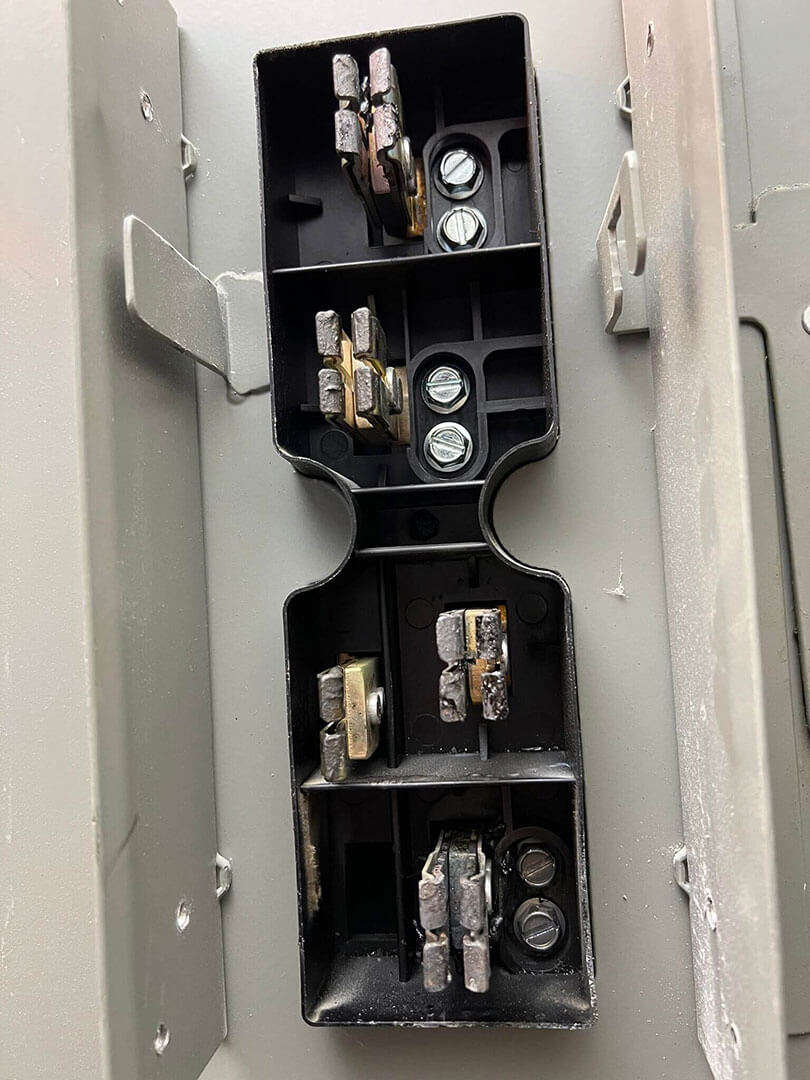
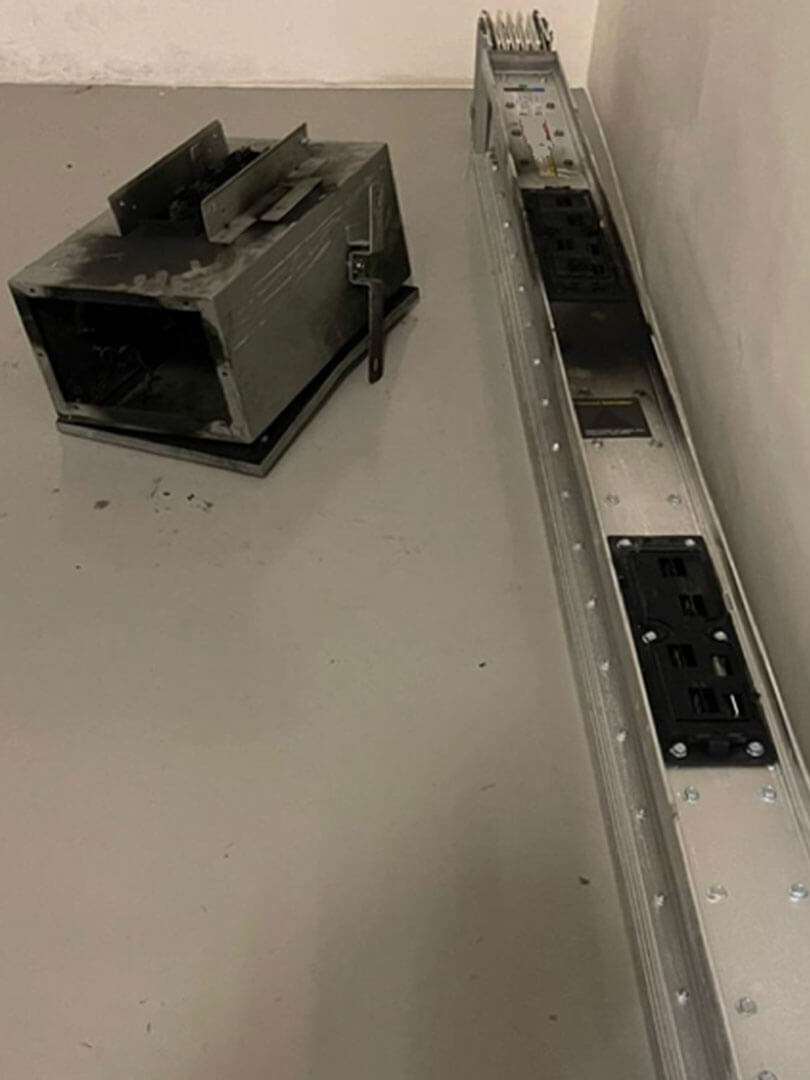
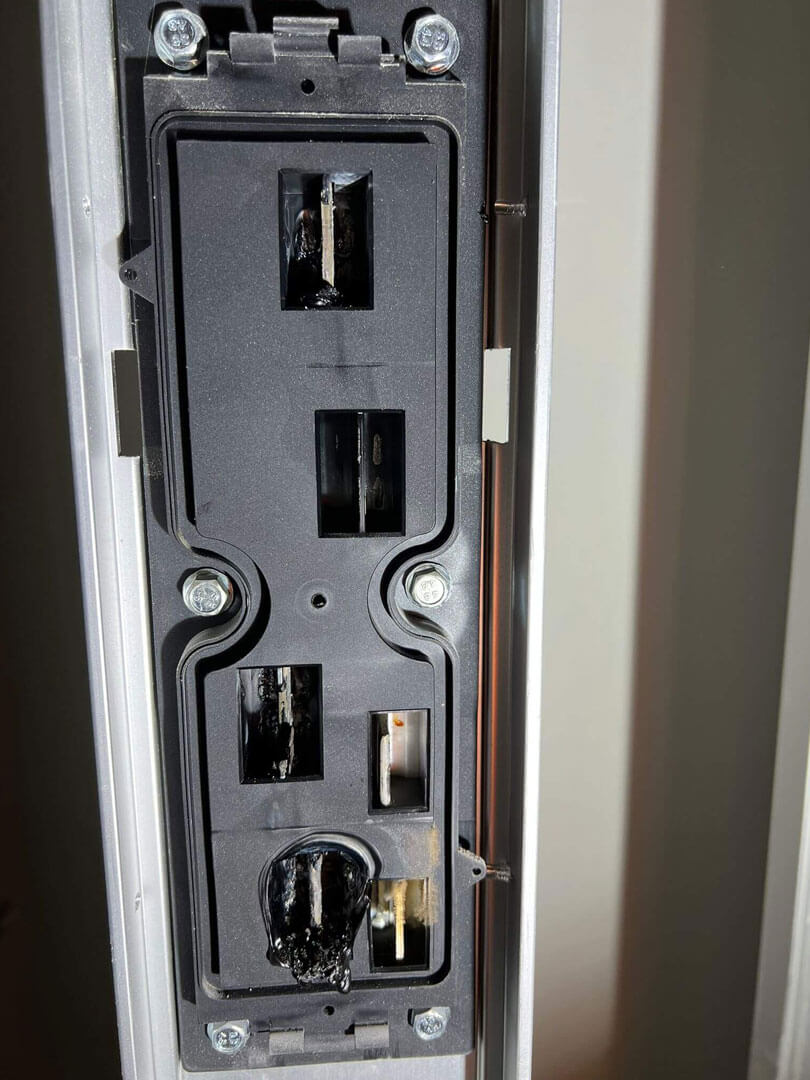
Melted Tap-Off Unit Joint
Bus bars can be joined in many different forms. It is important that they are well bolted, clamped, or welded to each other, or with other apparatuses, or else abnormal heating can occur at that location due to an increase in the electrical resistance if a bolt or clamp comes loose or a welded joint fails. This event of overheating may lead to an increase in electrical resistance and can lead to severe damage to machines or even a fire.
A regular inspection check is recommended, especially in the semiconductor plant, to prevent it from overheating or melting due to high heat. Many operators face difficulty as the bus bars are difficult to locate visually as they are often inside plastic or metal bus ducts with covers.
The burning out of a power supply bus bar is a threat to the semiconductor industry and other data centres as any unplanned shutdown of operations can cause a huge loss of production revenue.
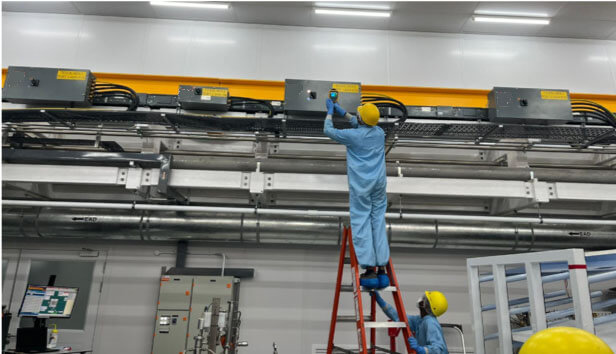
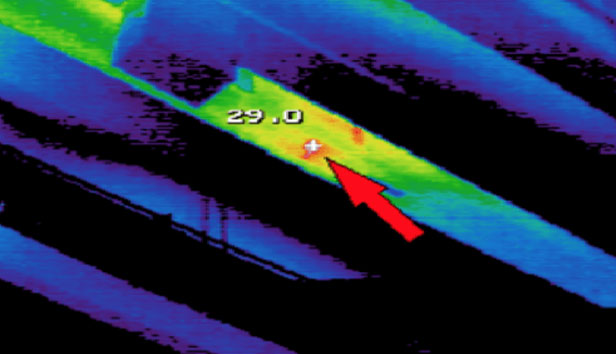
Existing Solution to Measure Temperature
Based on the IEC standard evaluation, some method to check the stability of the bus duct and other power distribution systems is the evaluation of a “permissible temperature”.
Therefore, any abnormality of a product can be detected just by checking the temperature change.
Available solutions out in the market;
1. Distributed Temperature System
- Optical Fiber Cable Sensors: Effective but costly to implement.
2. Infrared or Thermal Imaging
- Bus bars follow complicated paths through plant structures and other types of buildings. They may have a number of blind spots that cannot be readily captured using thermal imaging cameras
- Battery-operated Digital Temperature Sensor or Thermocouple are not suitable as bus bars are surrounded by strong electric fields
The Results
Solution using
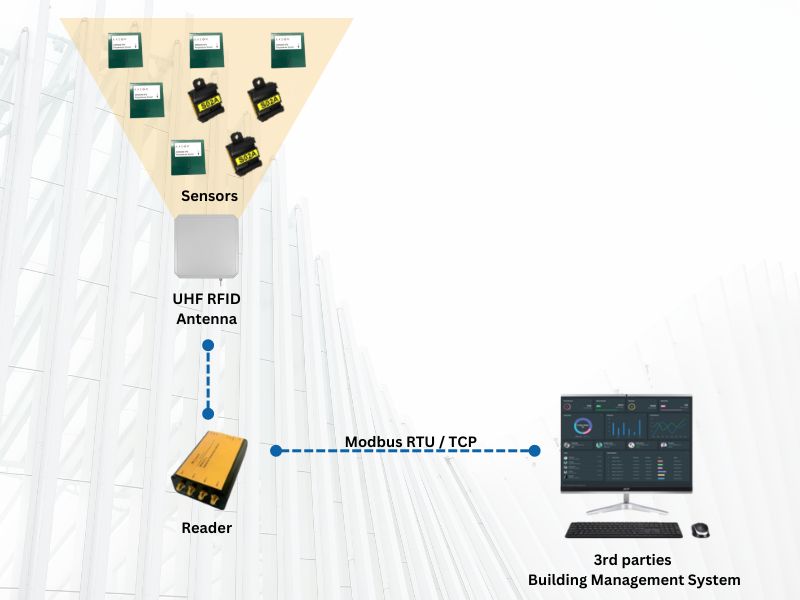
The LKH Axzon empowers you with 24/7/365 condition-based monitoring for predictive maintenance using our wireless, battery-free temperature sensors. Smart Passive Sensing™ technology makes it simple to monitor thermal conditions in your equipment.
Smart Passive Sensing™
The sensors which come in small and compact form are allowed to fit almost anywhere so that they are able to provide full coverage that covers the operators’ blind spots. Each sensor can be individually identified by the reader, allowing anyone who is maintaining the system to easily locate the source of any problem.
Our reader’s support communication protocols is necessary to link up the sensor data to a 3rd parties building management system platform where temperature alarms can be configured and monitored in real time.
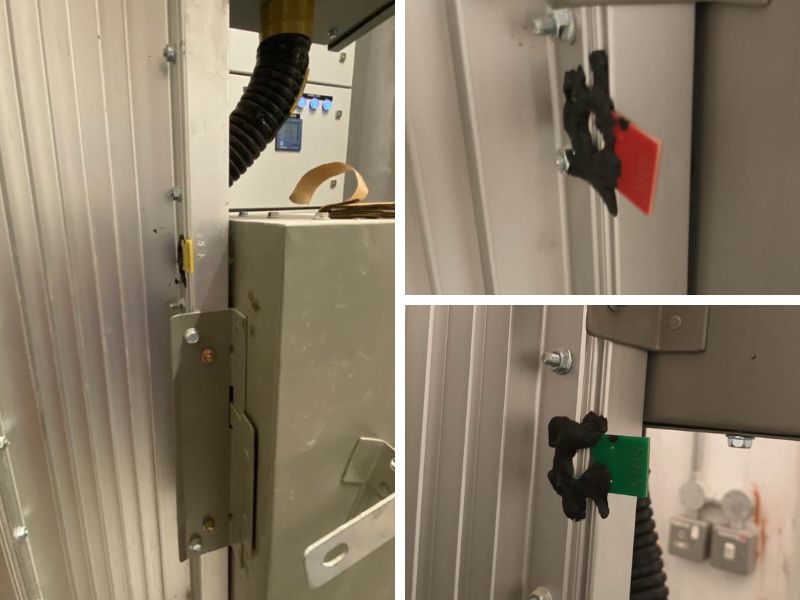
Wireless, Battery-Free Temperature Sensors
AZN 3130 Peel N Stick Sensors
AZN 3130 labels provide on-metal tag functionality with built-in temperature sensor as well as moisture detection within a low profile label. Supplied in roll form enabling low-cost and hassle-free RFID deployment. The consistency and reliability of the tag redefine the standard for on and off-metal RFID tagging, enabling new applications and revolutionizing integration into manufacturing and supply chain processes.
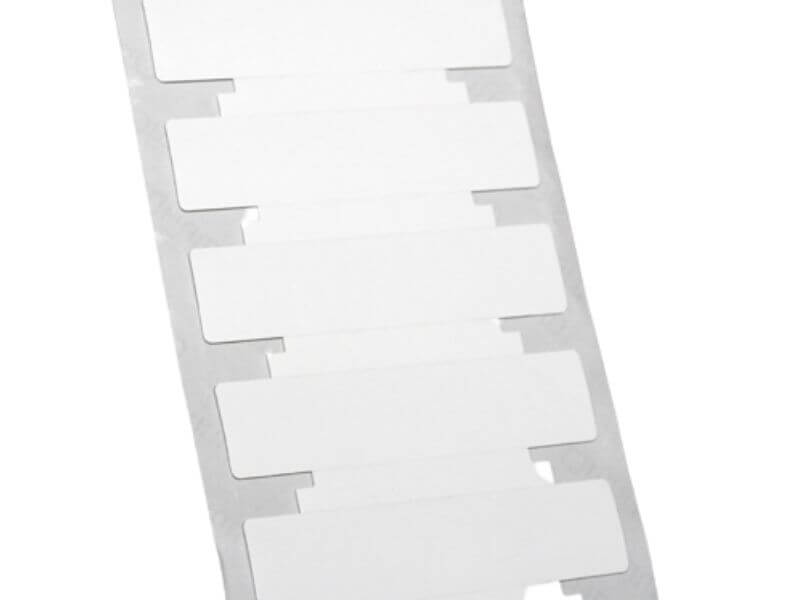
Peel N Stick Sensors
A successful predictive maintenance strategy requires reliable data about the condition of equipment at all times during the operation of the equipment. Continuous temperature monitoring from Axzon provides you with the most accurate and reliable temperature data that you need to detect unusual changes in the bus duct heat signature.
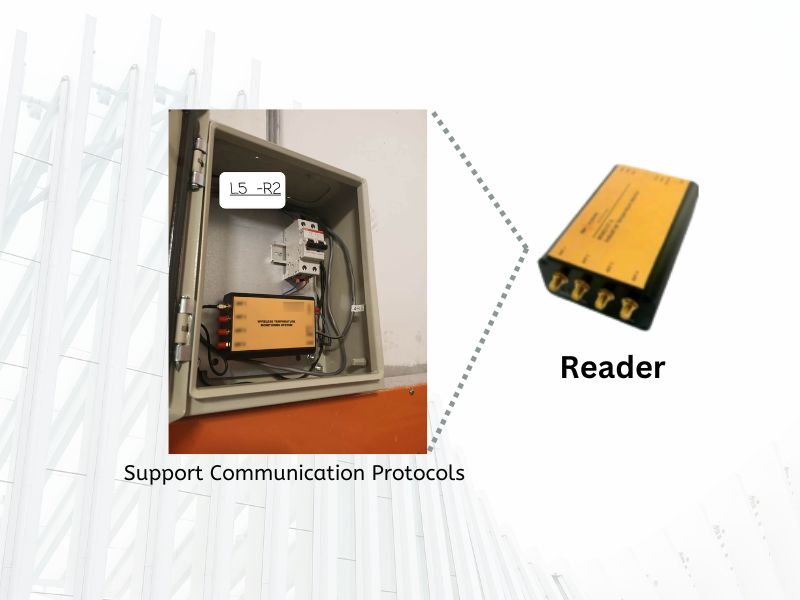
Collection of Sensor Data
The Benefits
- Comprehensive sensing coverage for the complex extended structure
- Detection of abnormal temperature to prevent burnout
- Continuous condition-based inspection work to detect an abnormal rise in temperature
- Monitoring of temperature under a strong electric field
Read more about the Building Management Systems that we provide.
Interested to find out more about Building Management Systems? Feel free to contact us!