Achieving Carbon Neutrality Through Efficient Facility Maintenance
Carbon neutrality involves balancing greenhouse gas emissions and their removal, like through forest management, for a net zero carbon footprint. In this document, Volume 5 of our Predictive Maintenance Solutions series, we explore achieving environmental and business objectives through efficient facility maintenance.
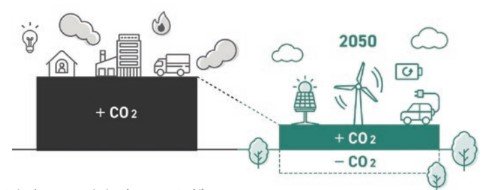
The Global Pursuit of Carbon Neutrality
Given the numerous recent weather disasters worldwide, addressing greenhouse gas emissions has gained global attention. The Paris Climate Agreement mandates signatory countries to reduce emissions and achieve carbon neutrality by the latter half of this century. These countries have set ambitious 2050 goals, sparking a global race toward carbon neutrality.
Why the Manufacturing Sector Should Work Toward Carbon Neutrality
Manufacturing contributes significantly to global energy-related CO2 emissions, emphasizing the substantial impact of carbon neutrality efforts in this sector. Factories, known for their high energy consumption and environmental footprint, require urgent improvements.
Achieving carbon neutrality by 2050 necessitates action across industries and departments. It’s essential for each company to find the right balance between energy conservation, renewable energy, and electrification for effective emission reduction. This document outlines steps for facility management focused on energy conservation.
- Power / fossil fuel sector: Expand use of renewable energy
- Transportation sector: Use renewable energy, e.g. by using electric vehicles
- Manufacturing and building sectors: Implement rigorous energy conservation measures, use renewable energy
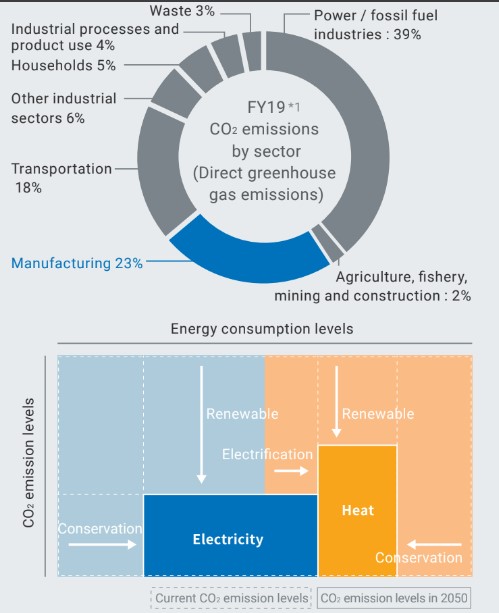
Efforts Towards Carbon Neutrality
Conserving Energy Using Localized Clean Room Environments
Due to its design, a clean room consumes substantial energy. Many manufacturing customers have effectively curbed energy usage by implementing scaled localized clean room setups tailored to specific processes, such as assembly and inspections.
Conserving Energy Using Inverters
In certain factories, entire production floors undergo air conditioning, resulting in substantial energy use. Some customers, including manufacturers, effectively curbed this consumption. They achieved this by adopting inverter fan motors and employing demand monitoring equipment for visualizing power consumption. This approach allowed them to optimize production equipment operation schedules, such as distributing break times more efficiently.
Our Commitment to the Environment
Indicators and Targets
Omron’s “Carbon Zero” initiative sets the goal of reducing greenhouse gas emissions to zero by 2050. Using the Scope 1 and 2 *1 greenhouse gas emission quantities of fiscal 2016 as a baseline, we backcast from fiscal 2050 to set reduction targets for fiscal 2030 and fiscal 2020.*2 We are currently taking several measures to meet these goals.
For example, in fiscal 2018, we began using electricity sourced from renewable energy for our Japanese locations.
In fiscal 2019, we analyzed the energy conservation potential*3 of our locations in the Asia Pacific region, where we consume the third largest amount of energy, after Japan and China. In our Indonesian plants, we identified areas where annual energy consumptions could be cut by 23%, and are taking action based on a medium-term plan aimed to address these issues.
In fiscal 2020 we implemented energy conservation measures in several of our locations and built new solar power generation systems. We also analyzed the energy conservation potential of our plants in Malaysia, which consume large amounts of energy. As a result of these efforts, in fiscal 2020, we were able to reduce greenhouse gas emissions by 124kt-CO2, or by 50% compared to fiscal 2016. Omron will continue to work to reduce greenhouse gas emissions, toward our goal of net zero by 2050. We are currently developing our next long-term vision, which will include targets for Scope 3*1 emissions as well.
*1. Scope 1: Direct greenhouse gas (GHG) emissions. Direct GHG emissions occur from sources owned or controlled by the company, for example, emissions from combustion in owned or controlled boilers, furnaces, vehicles, etc.
Scope 2: Electricity indirect GHG emissions. Scope 2 accounts for GHG emissions from the generation of purchased electricity consumed by the company. Purchased electricity is defined as electricity that is purchased or otherwise brought into the organizational boundary of the company.
Scope 3: Other indirect GHG emissions. Scope 3 is an optional reporting category that allows for the treatment of all other indirect emissions. Scope 3 emissions are a consequence of the activities of the company, but occur from sources not owned or controlled by the company.
*2. Greenhouse gas emissions are calculated from sales forecasts, including the Automotive Electronic Components Business (AEC) that was sold off in October 2019. In considering targets to align with the SBT criteria in fiscal 2017, we set 2016, the year of the latest values, as the reference year.
*3. OMRON’s unique approach to identifying energy loss risks and opportunities for improving energy efficiency at production locations, formulating specific measures with estimates of impacts and costs.
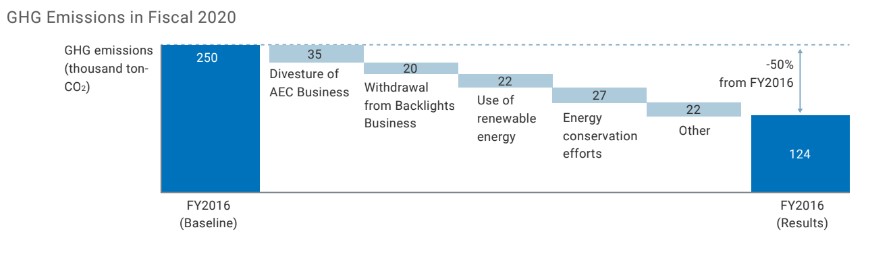
Achieving Both Environmental and Business Goals
Historically, businesses prioritized goals over the environment. Now, they must balance both. Facility maintenance poses challenges but benefits from technological advancements, offering solutions that harmonize environmental and business objectives.
Issues in Facility Maintenance
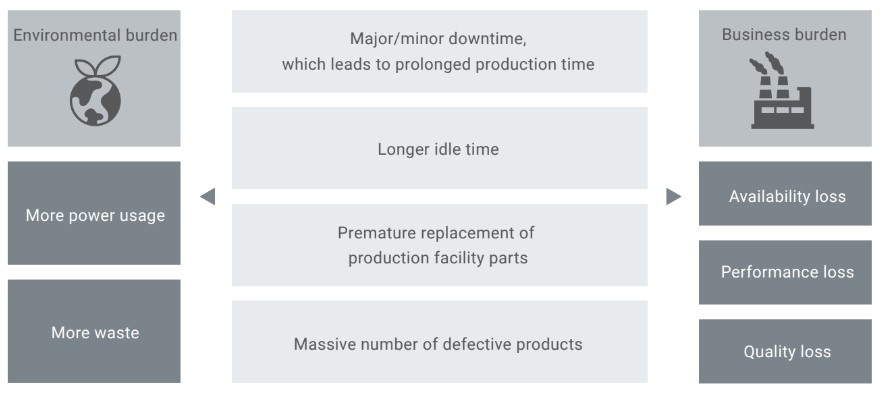
Two Types of Failures That Cause These Issues
Mainly, two types of facility failures, no-function and less-function, cause the mentioned issues. Efficiently preventing these failures is crucial to meet environmental and business goals concurrently.
No-function failure
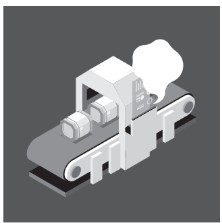
Failures leading to production facility shutdowns significantly impact overall energy efficiency in production operations.
Less-function failure
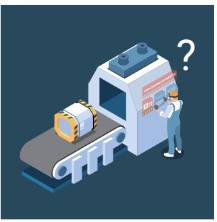
Production facility failures significantly impede production, reducing efficiency and increasing the disposal of defective products, ultimately resulting in energy wastage.
The thinking behind ISO14001
Efforts to treat waste and conserve energy excessively can harm a company’s business, rendering them unsustainable. To achieve both environmental and business objectives, aligning them is vital. ISO14001, an international environmental management systems standard, advises organizations to balance environmental protection with social needs and adapt flexibly to changing environmental conditions.
Preventing Failure by Switching to Predictive Maintenance
Maintenance encompasses three primary styles: reactive, preventive, and predictive. Reactive maintenance addresses failures post-occurrence, incurring environmental costs. Preventive maintenance relies on manual inspections, causing facility outages and premature part replacements. Consequently, organizations turn to technology-driven predictive maintenance.
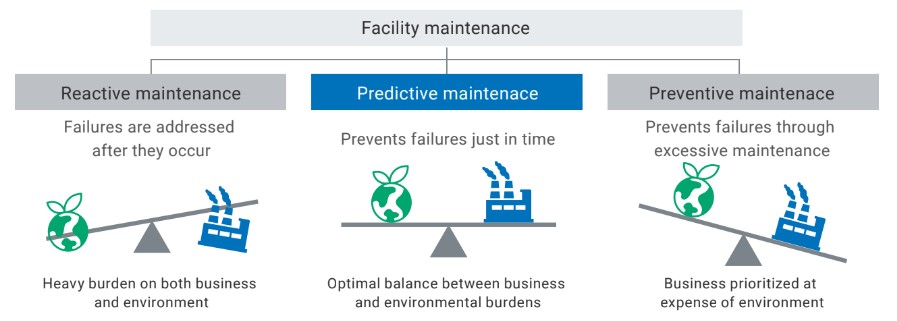
Conserving Energy through Predictive Maintenance
Predictive maintenance reduces failures and inspections, effectively reducing energy consumption. According to “Economics of Manufacturing Machinery Maintenance” (June 2020) by Douglas S. Thomas and Brian A. Weiss, implementing predictive maintenance could save 0.8 billion USD in defects and 18.1 billion USD in downtime. This environmentally-friendly approach aims to eliminate losses.
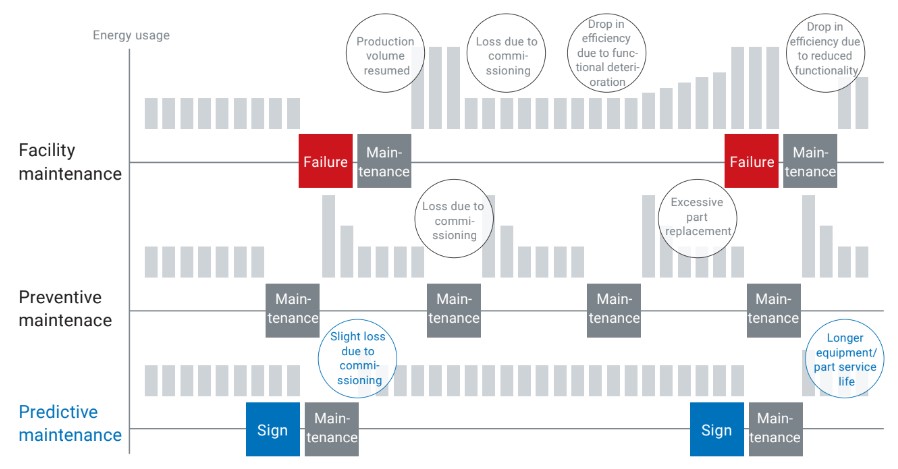
Omron’s Predictive Maintenance
Omron’s predictive maintenance solutions encompass data collection, visualization, analysis, and on-site condition monitoring, enabling department-level implementation.
Power must never be stopped; critical facilities need advanced anomaly detection
Power, which transforms energy (like electrical energy) into heat or force, drives machinery like motors and heaters. Control panels oversee them. Facility halts when power fails, severely impacting production. Thus, power, akin to the human heart, must never cease. Understanding failure causes and continual deterioration monitoring are crucial.
Solutions for preventing no-function power failures
Our solutions digitize information about power component deterioration to prevent facility failures. This enables the early detection of motor bearing and insulation issues, which are energy-intensive, as well as abnormal facility temperatures that result in energy waste.
Products for monitoring the conditions of 3-phase induction motors and their peripherals
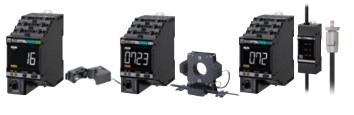
Products for monitoring the trend of insulation degradation in motors
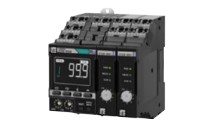
Products for monitoring the temperature conditions of devices and equipment
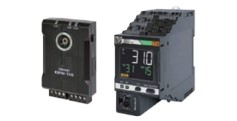
Products for monitoring the voltage, current, and remaining life of switched-mode power supplies
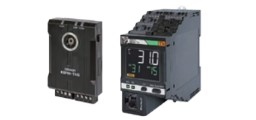
Monitoring all fluid components, moving parts, environmental components, and workpieces to maintain excellent health
Electric currents, liquids, gases, and fluids traverse wiring and piping, while moving parts use energy to process objects. Monitoring these components, alongside workpieces and environmental factors, allows for identifying changes in facility conditions and establishing causal links. In a human body analogy, these components resemble blood, muscles (joints), and the living environment. This monitoring is akin to a physical examination, assessing a person’s health and lifestyle to uncover problems and potential solutions.
Condition sensing for preventing less-function failures
To maintain facility health and prevent malfunctions, digitization captures changes in component conditions (fluids, moving parts, environment, workpieces). This ensures quality stability and optimizes energy efficiency.
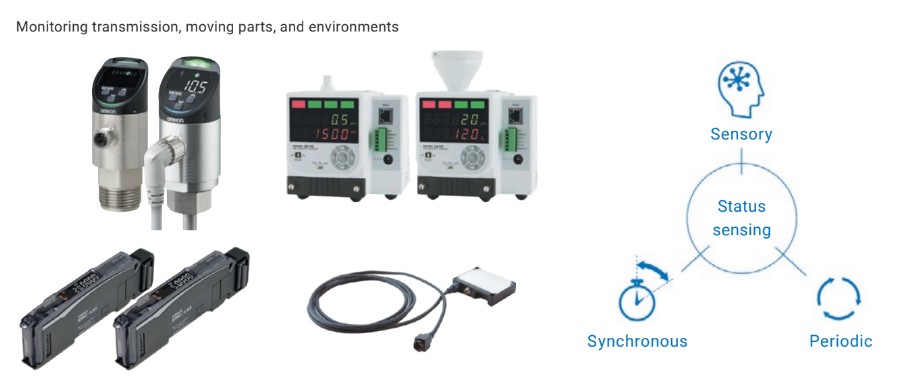
Electric Power Monitoring Solutions
To attain carbon neutrality, it’s crucial to visualize power consumption, both per production line and equipment, and for the entire plant. This helps identify energy-intensive lines and equipment for targeted improvements. Our KM Series products enable comprehensive electric power monitoring, enabling this visualization.
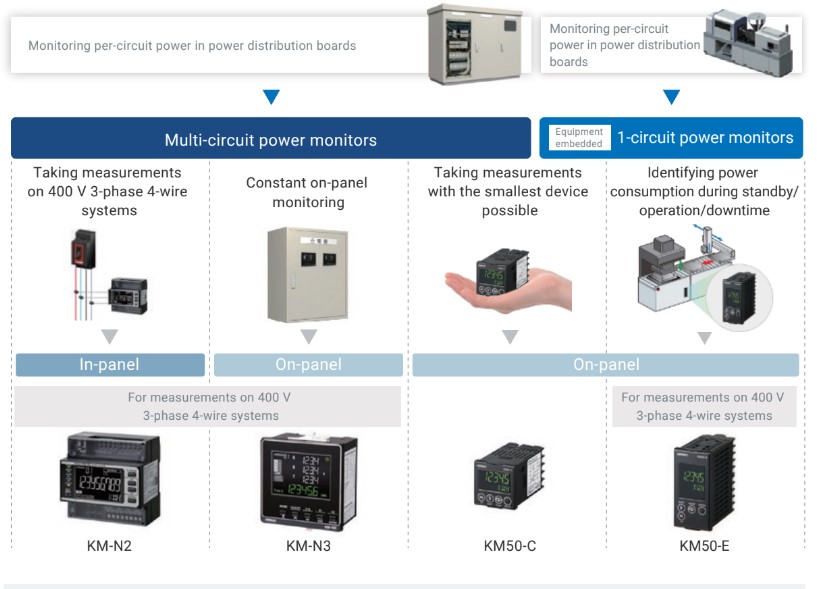
The Continuing Evolution of Maintenance Innovation Solutions
Business planning with an eye toward energy management
We are actively developing innovative maintenance solutions, enabling our customers to proactively manage energy in their plants and supply chains. To achieve this, we engage in open innovation partnerships with various companies.
Use Cases: Reducing Loss Through Maintenance Innovation
- Optimizing Water Use in Fusion Furnace by Simultaneously Monitoring Flow Rate and Temperature
- Reducing Disposals Due to Contamination in Beverage Manufacturing Process
- Reducing Disposal Loss by Preventing Power Failures
- Reducing Energy Loss in Drying Oven by Monitoring Duct Conditions
Background:
The increasing emphasis on SDGs and ESG management has led to more stringent factory wastewater regulations, compelling manufacturers to limit resource consumption. This is particularly critical in facilities with high water-consuming equipment like glass fusion furnaces. In one case, operators continuously monitored cooling water quantity and temperature in shifts, disposing of excess water. The optimal flow rate remained uncertain, resulting in significant water wastage.
Implementation:
The IoT flow sensor (E8FC) detects flow rate and temperature concurrently. It enables operators to ensure the optimal temperature and flow rate of water, allowing for valve adjustments as required. Although a comparable solution using mass flow meters exists, it is costly. Consequently, the customer chose our system, expecting a more favorable return on investment.

Impact:
It offers insights into the health of fluid components, ensuring a steady supply of efficiently temperature-controlled cooling water. This not only conserves water but also prevents quality issues, illustrating the simultaneous attainment of environmental and business objectives.
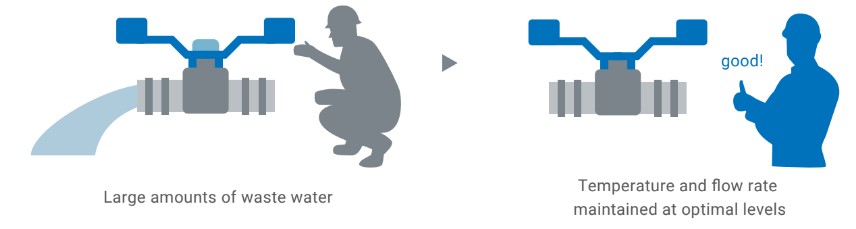
Background:
Worn piston seals caused foreign matter contamination, necessitating lot disposal. To align with business goals, preventive maintenance was adopted. However, frequent part replacements during production downtime increased energy consumption.
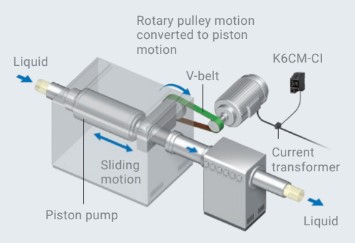
Implementation
Omron’s condition monitoring device was tested on existing equipment, results shared across factories. A decision followed to employ a similar device in a new factory’s remote monitoring system, promoting IoT. The customer plans to expand this system to existing equipment in other factories, continuously evaluating its effectiveness.
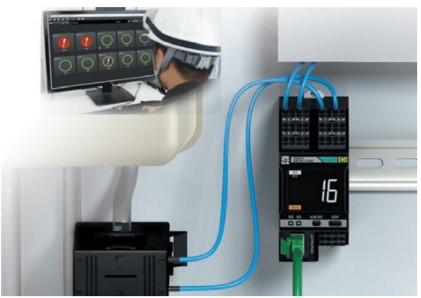
Impact:
It identifies seal deterioration, preventing beverage contamination and reducing mass disposal. Additionally, it conserves energy by replacing parts based on actual conditions, reducing waste and scheduled repairs.
Background:
In metal processing machines, like those used for cutting, cutting oil mist can infiltrate equipment, accelerating insulation deterioration. This can result in production stoppages, causing energy waste and potentially leading to more severe issues, including smoke or ignition accidents.
Implementation:
Previously, insulation resistance measurements fluctuated over time. Installing an insulation resistance monitoring device (K7GE) enabled real-time data accumulation, revealing the impacts of temperature, humidity, and manual measurements on accuracy and highlighting the device’s potential to enhance maintenance operations.
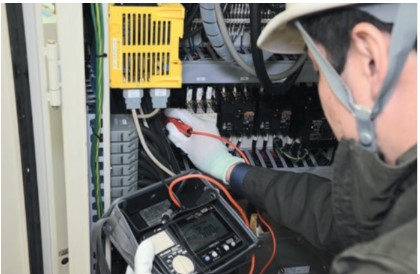
Impact:
By utilizing insulation resistance meters, it reduces inspection effort, allowing systematic maintenance by identifying insulation deterioration trends. This proactive approach helps prevent unexpected failures, saving energy resources.
Background:
Thermal degradation resulted in hot air leakage from a car paint-drying oven’s ducts, affecting drying quality and energy efficiency. Maintenance workers had to risk their safety by approaching the ducts regularly to monitor them with thermoviewers.
Implementation:
The thermal condition monitoring device (K6PM-TH) was installed on operational equipment to study temperature changes during hot air leaks. The findings were shared with various plants, prompting interest in adopting the device. Eventually, it was incorporated into a remote monitoring system for a new plant under construction. This predictive maintenance system aligns with the company’s IoT initiative and integrates Omron’s condition monitoring devices with power monitoring equipment and environmental sensors.
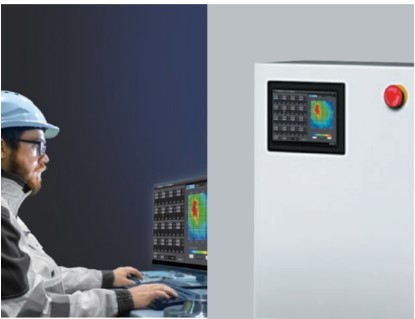
Impact:
Enhances efficiency by reducing manual tasks and simplifying maintenance. Continuous monitoring devices provide real-time insight into energy conditions, enabling quick detection of hot air leaks and proactive maintenance. The customer plans to evaluate the solution’s effectiveness before expanding it to other plants.
Omron’s Co-Creation Services
The Continuing Evolution of Predictive Maintenance
The solutions mentioned are “site-contained,” meaning they address issues within the manufacturing site, allowing for easy small-scale implementation. The next phase involves optimizing the entire factory by connecting various equipment for broader predictive maintenance. Our co-creative services offer tailored solutions for your specific requirements.
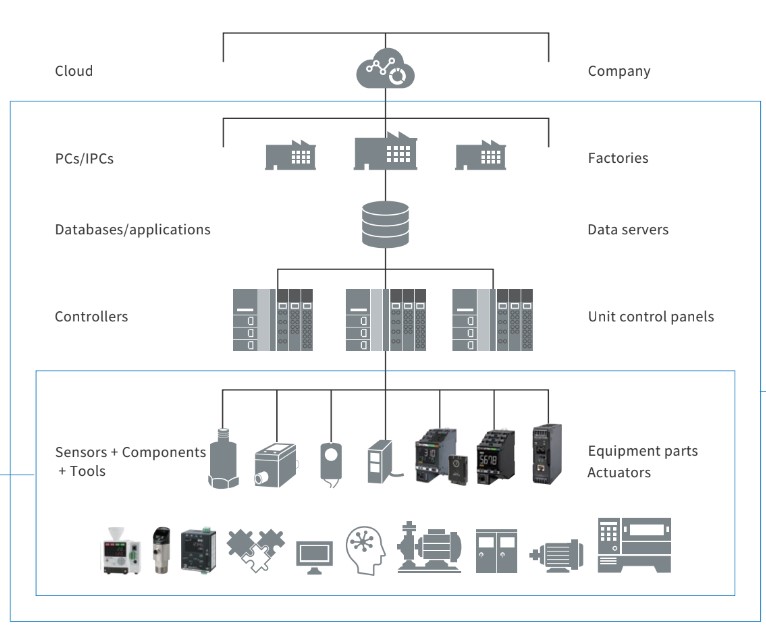
Site-Contained Solutions
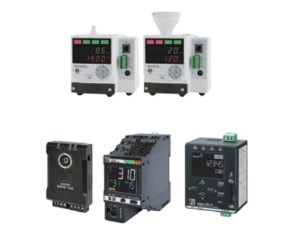
On-Site Data Utilization Service
Omron’s i-BELT services are co-creation services that offer close support for addressing issues in visualization, analysis, and control. They utilize data collected from the production site.

On-Site Data Utilization Device
To streamline energy usage and significantly reduce consumption, it’s crucial to utilize on-site data effectively. i-BELT facilitates this by digitizing information from sensors and components, drawing on our extensive control experience in FA sites, and applying advanced technologies. This service employs logical and scientific approaches to address management challenges and supports customers in digitally transforming their production sites into data-accessible and user-friendly environments.
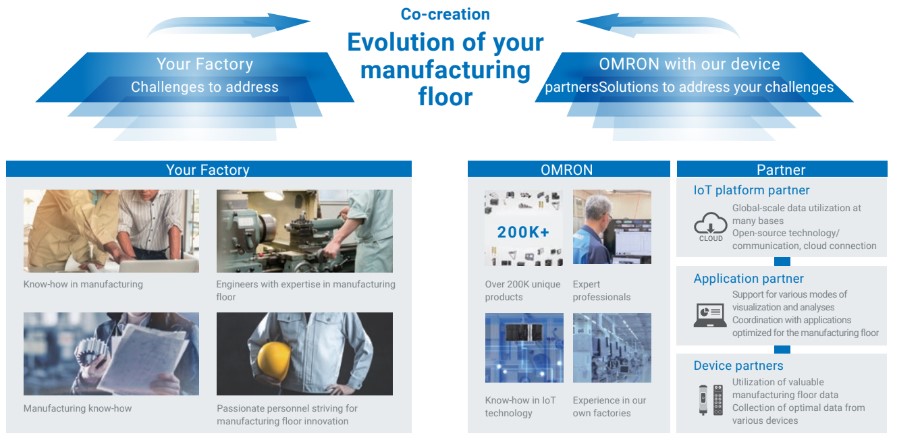
Co-creation working closely with you
We collaboratively set project goals through discussions and work with you to resolve manufacturing floor challenges using data-driven insights.
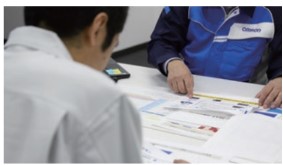
Formulation of challenges based on data
We collaboratively set project goals through discussions and work with you to resolve manufacturing floor challenges using data-driven insights.
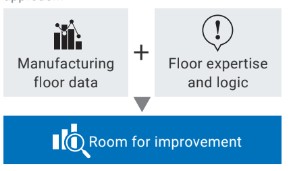
Firm advancement of innovations in phases
We offer assistance in achieving your goal through a multi-stage floor innovation approach, ensuring results after recognizing the scenario.
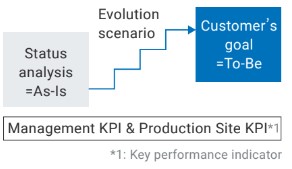
Energy Management Service
We support energy management with a focus on power usage, helping achieve zero waste from equipment to the entire factory in the manufacturing process.
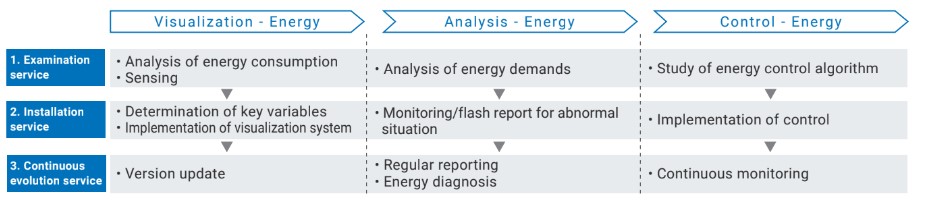
i-BELT Use Cases
- Optimization of air compressor setting pressure
- Reducing Energy Loss by Optimizing Equipment Operation Time
Background:
Identifying power consumption during standby/operation/downtime
Implementation:
Visualization: Gathering data on production, quality, and facility operations.
Analysis: Comparison analysis with the target value and reference value
Detected pressure loss occurring in compressed air piping in multiple locations of production facility.
Control: Energy control linking production floor with facility
Achieving optimized control without waste through real-time predictive compressor control based on manufacturing floor usage.
Impact:
Reduction of compressor power consumption by 18%
Furthermore, aside from energy conservation, the solution also alleviated pressure drops in devices that had been causing energy loss, consequently reducing minor equipment downtime attributed to energy fluctuations.
Background:
Customer wanted to reduce factory power consumption by optimizing power usage.
Implementation:
Visualization: Visualizing equipment energy conditions
We affixed sensors to various devices to identify elements with potential for effective improvement.
Analysis: Batch analysis of electric power and equipment behavior
Discovered that equipment running round the clock could be halted during specific time intervals.
Control: Automatic energy conservation
We identified opportune moments for halting equipment without affecting production and implemented automated energy conservation by incorporating eco-mode control features into the equipment.
Impact:
Cut energy use by 23% across all factory equipment
Automatic power saving was accomplished by identifying moments when equipment could halt without affecting production and incorporating eco-made features
To monitor the condition of 3 phase induction motors and peripheral equipment
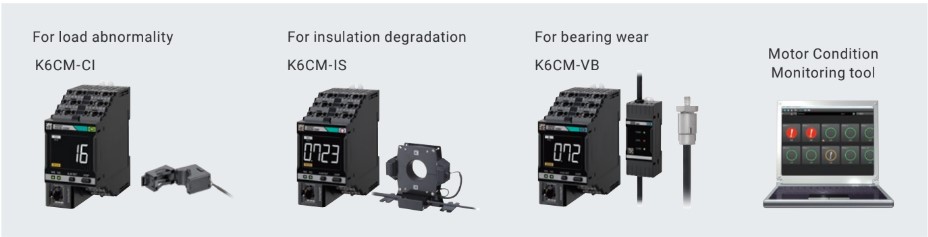
To monitor the trend of insulation degradation in motors
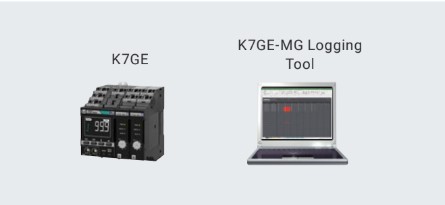
Products for monitoring fluid components, moving parts, and environments
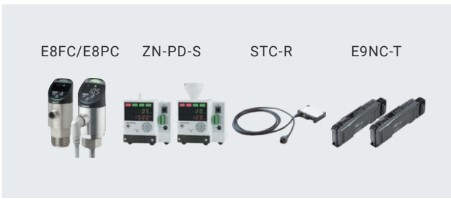
To monitor the temperature status of devices and equipment
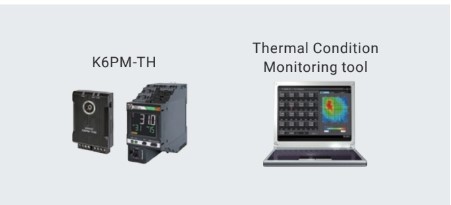
Products for monitoring power usage and identifying problems
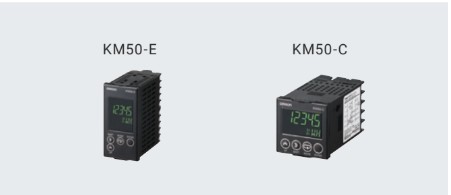
Interested to find out more about Carbon Neutrality with Facility Maintenance? Feel free to contact us!