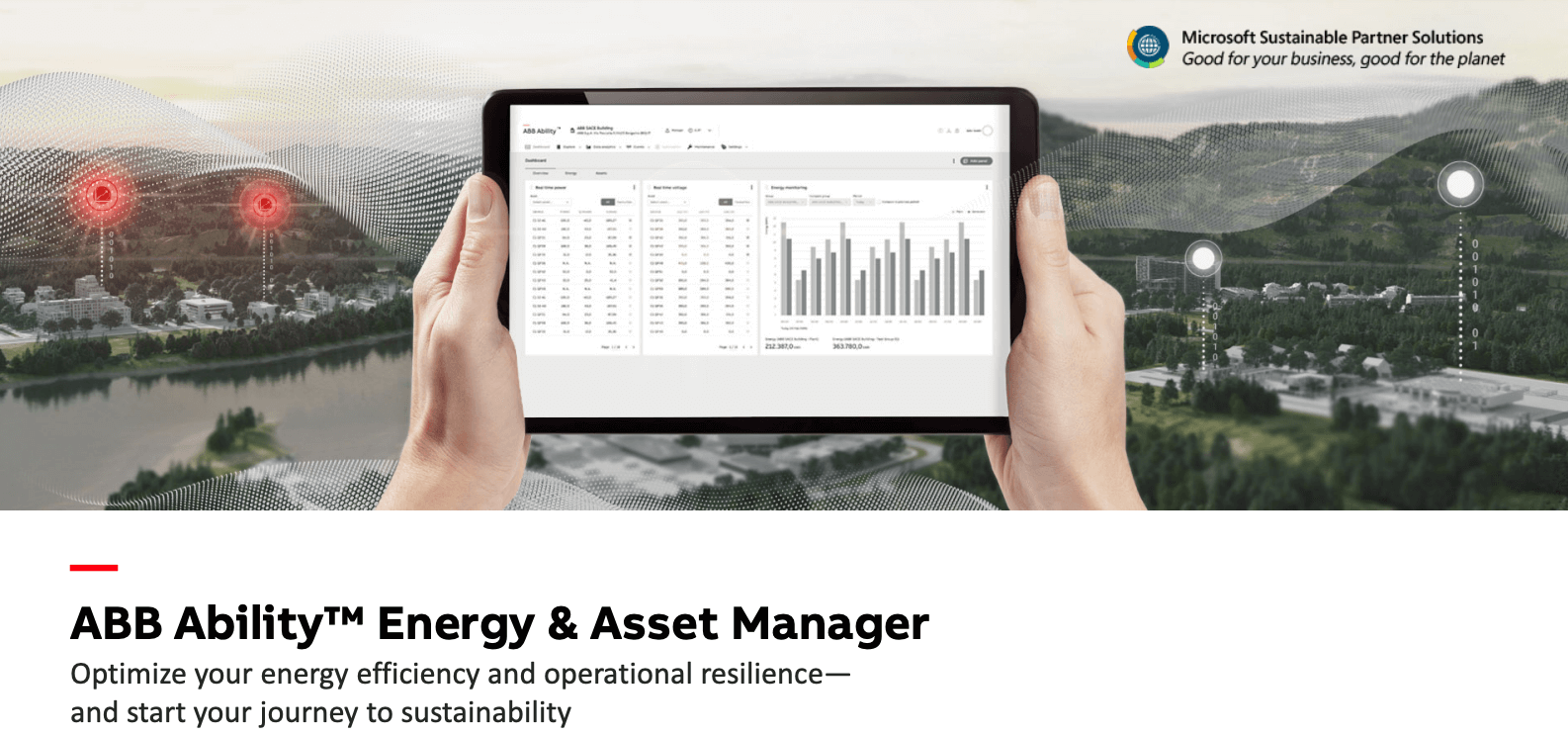
Help the planet– and your bottom line
The demand for electrical energy is expected to increase 33% by 2040 due to a rise in urbanization and industrialization. At the same time, CO2 emissions have risen by almost 50% since 1990, leading to increasingly warmer temperatures every decade since the 1960s. The impacts of this climate change include extreme weather events and food supply disruptions.
Becoming part of the solution
To stay competitive, compliant, and socially responsible, organizations are recognizing the need to reduce their carbon footprint. Over 40 countries and more than 20 cities, states and provinces are already taxing companies on the amount of carbon pollution that they generate. And 81% of global consumers feel that companies should help improve the environment.
Sustainable development means progress towards a healthier and more prosperous. This means balancing the needs of society, the environment, and the economy. To achieve this, organizations need to embed this approach to business across their value chain, creating superior value for all stakeholders.
Let’s take a good look at how Oppo and Frosinone use sustainable solutions to boost their business.
OPPO’s Success Case Study
Efficiently powering the future of 5G
Situation
Oppo, one of the world’s largest manufacturers of mobile devices and a growing global 5G player, needed to ensure reliable, energy-efficient power supplies for its new, state -of the-art technology park in Chongqing, China. The campus was developed to support OPPO’s ambition to build a range of smart products and services around smartphones and lead industrial development in the 5G+ era. Production at the site is expected to exceed more than 30 billion RMB (USD 4.5bn) annually in value and create tens of thousands of jobs.
Solution
Oppo chose to install the ABB Ability™ Energy and Asset Manager to monitor, operate, and maintain its power distribution system. Site managers have access to continuous, real-time insights on the operating condition of power equipment. Operations and maintenance teams receive automatic alerts so they can proactively address issues, helping to optimize performance and maximize uptime.
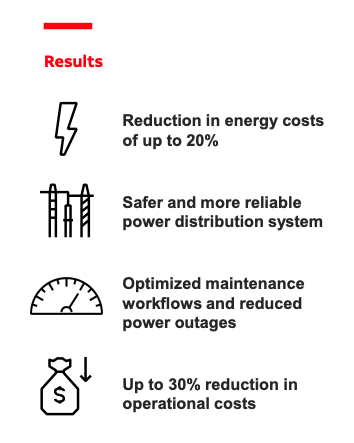
Frosinone’s Success Case Study

Unlocking cost and carbon savings
Situation
Frosinone is a global production hub for ABB’s low-voltage circuit breaker technologies. The factory, along with sister plants in Dalmine and Santa Palomba, is Lighthouse Plants, selected by the Italian government as a model for other companies working on digital transformation and Industry 4.0 strategies. With an annual power consumption of 9000 MWh and an energy bill in the region of €1.2 million, the facility team wanted to explore opportunities for reducing costs and carbon emissions using digital energy management and renewables.
Solution
As the first step in their sustainability strategy, ABB Frosinone implemented a retrofit switchgear upgrade that was connected to the cloud-based ABB Ability™ Energy Manager solution (formerly known as EDCS). The new system was able to monitor more than 120 electrical distribution points at the facility, helping staff continuously improve the site’s energy efficiency and power asset management. Advanced algorithms and machine learning helped Frosinone identify hidden drains on the site’s energy, as well as calculate the payback period for any investment in new equipment.
“We make technologies that help customers save energy – so we want the manufacturing to be as sustainable as possible.” – Massimiliano Cifalitti, ABB Hub Europe Manager
MORE INTERESTING CASE STUDIES
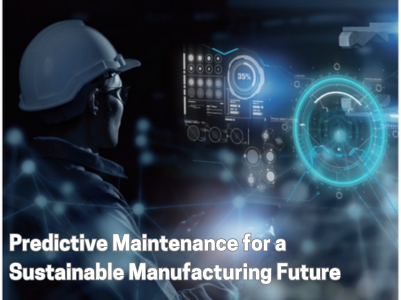
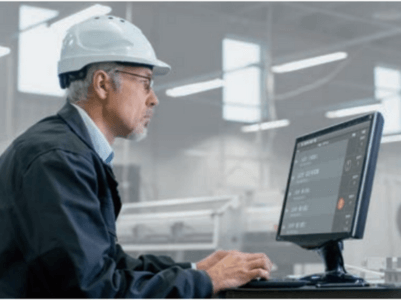