To the Era of Predictive Maintenance
The manufacturing industry is transitioning to predictive maintenance due to digital technology advancements and COVID-19’s impact. This overview explains predictive maintenance and its growing adoption.
What is Predictive Maintenance?
Predictive Maintenance differs from conventional scheduled maintenance, relying on real-time 24/7 equipment condition monitoring. Companies offer solutions through cloud or edge computing systems, enabling anomaly detection. This approach minimizes unexpected downtime, lowers excess part replacement expenses, and addresses labor shortages.
Background for the Advancement of Predictive Maintenance
Global COVID-19 Pandemic
Drs. Michael P. Brundage and Brian A. Weiss from the National Institute of Standards and Technology (NIST) in the USA emphasize the need for factories to adapt to the 2020 global COVID-19 pandemic by implementing a more efficient factory operation system. This system should enable continued manufacturing with fewer personnel, in line with the requirement for reduced in-person work through personnel relocation and reduction. In their report, they propose Prognostics and Health Management (PHM) as a solution to this challenge. PHM encompasses various new technologies and methodologies, including predictive maintenance, aimed at addressing management challenges like achieving zero downtime and controlling quality deterioration. These techniques involve detecting equipment failures, pinpointing failure locations, conducting diagnostic tests, and estimating remaining equipment life.
Increased Importance of PHM Technologies
Reducing in-person work through staff relocation and downsizing may decrease equipment maintenance frequency. However, PHM optimization can enhance efficiency, even with fewer personnel. For example, automated monitoring allows maintenance staff to focus on other tasks, while improved data analysis reduces task times like root cause analysis. More precise failure prediction prevents over-maintenance and under-maintenance, streamlining schedules. PHM, monitoring real-time production, offering equipment history, and predicting potential failures, reduces maintenance time and costs. In 2016, American manufacturers spent $50 billion on maintenance, a substantial portion of total operating expenses. PHM improves equipment availability, reduces failures, and maintains process quality. Manufacturers can effectively use PHM to determine suitable levels of reactive, preventive, and predictive maintenance. Even a minor PHM improvement can optimize strategies, minimize downtime, and save expenses.
Predicting the Future of Maintenance from the SINIC Theory
Shifting our perspective, we can envision the future of maintenance through the SINIC theory,
Omron’s guiding principle. The “SINIC theory,” introduced by Omron’s founder, Kazuma Tateishi, in 1970, accurately foretells societal trends up to the mid-21st century, including the Information Society’s emergence, despite being conceived during a pre-PC and pre-Internet era of rapid Japanese economic growth.
SINIC, or Seed-Innovation to Need-Impetus Cyclic Evolution, posits a cyclical relationship among science, technology, and society. Scientific advancements lead to new technologies that drive societal progress, while societal needs stimulate technological development and anticipations of scientific breakthroughs. This mutual influence forms a continuous cycle, propelling further social evolution.
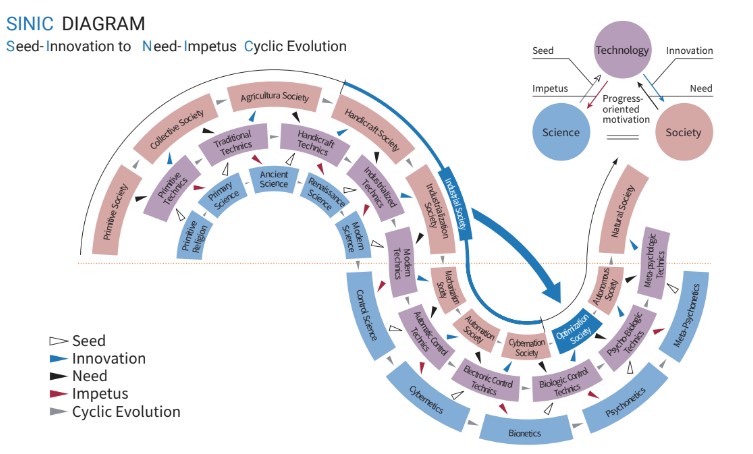
Predictive Maintenance applied to “optimization society”
This theory defines the present as an optimization society, where a harmonious balance between “individual and society,” “humans and nature,” and “humans and machines” is pursued for spiritual enrichment. One emerging trend in maintenance is the adoption of predictive maintenance, which Omron believes can lead to reduced unexpected maintenance workload, eco-friendly practices through reduced disposal, and the promotion of sustainable human and machine development. These advancements contribute to the cultivation of spiritual wealth and new ways of living.
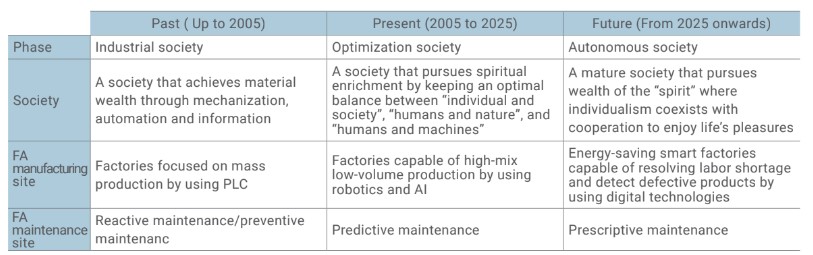
Issues of the Preventive Maintenance and Benefits of the Predictive Maintenance
Preventive maintenance, traditionally favored for its affordability and simplicity, raises concerns for the manufacturing industry’s future sustainability. Challenges include labor shortages, skill transfer, and environmental impact. The subsequent sections will contrast these issues with the advantages of predictive maintenance.
Conventional Preventive Maintenance and its Issues
In the manufacturing industry, many adopt “Time Based Maintenance,” involving scheduled inspections and part replacements. This proactive approach minimizes equipment failures and allows planned maintenance. Moreover, skilled maintenance engineers often merge preventive and condition-based maintenance, assessing equipment during inspections to decide on part replacements based on their expertise. While preventive maintenance has evolved, certain issues have emerged.
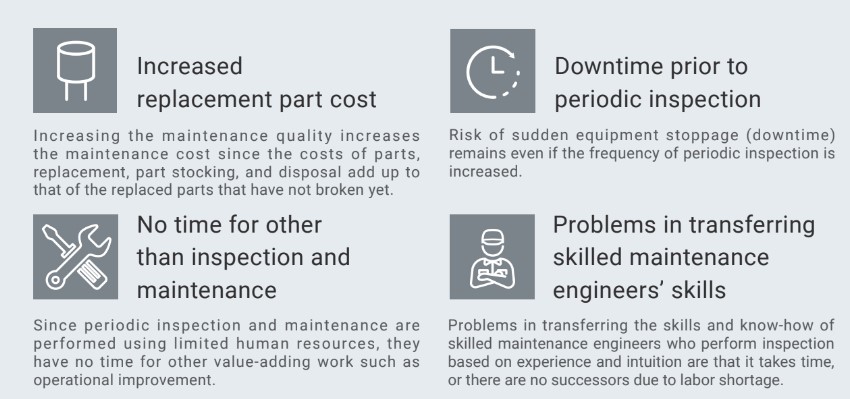
Predictive Maintenance is the Solution to Preventive Maintenance Issues
Timing of inspection in predictive maintenance
In preventive maintenance, inspection is performed in a planned manner,
independently of equipment failure. “Time Based Maintenance” causes excess part replacement and inspection expenditures. In predictive maintenance, inspection is performed when a sign of failure is captured. “Condition Based Maintenance” does not cause unnecessary part replacement and inspection expenditures.
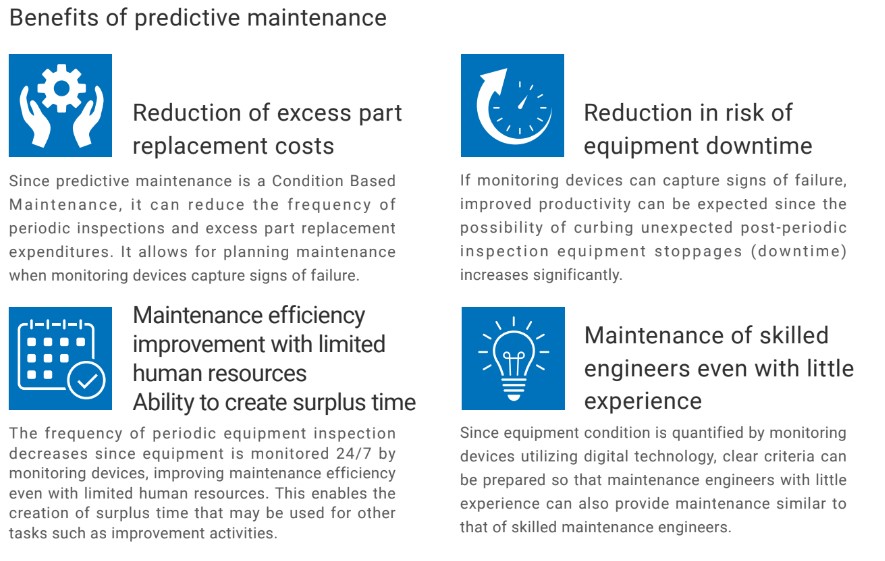
Omron’s End-to-end On-site Predictive Maintenance Concept
Two major factors slow the adoption of predictive maintenance despite its recognized benefits: the significant initial costs, including skill development, and the less obvious return on investment. Omron’s condition monitoring devices offer a cost-effective, manpower-efficient solution. They don’t necessitate extensive system design or data analysis, as they collect, analyze, and assess data on-site. This approach allows for a manageable starting point, enabling early ROI assessment before full implementation decisions.
From: Predictive maintenance system utilizing PLC and cloud

Hurdle to introduction is high because of technical and organizational barriers; requires difficult analysis as well as IT/OT integration.
To: End-to-end on-site predictive maintenance system utilizing Omron’s condition monitoring device

The low entry barrier stems from on-site analysis and visualization. Moreover, scalability is straightforward, and on-site ROI verification supports full deployment.
Image of Costs to Introduce Predictive Maintenance Utilizing Omron’s Condition Monitoring Device

Maintenance innovation by “condition monitoring” compatible with the new normal
The COVID-19 pandemic has accelerated the DX social trend via technological innovation. Omron aligns with the end-to-end on-site concept and introduces the 3 GEN principle: monitoring and analyzing GENbutsu (actual things) through data, assessing GENjitsu (reality) remotely, and acting at the GENba (actual site) as needed. Omron provides straightforward component-level on-site condition monitoring solutions for quick adoption.

Extra value brought about by Omron’s maintenance innovation solutions
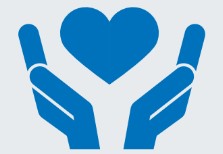
Safety
Automating maintenance in high-risk areas, like elevated, high-voltage, or high-temperature sites, mitigates employee accident risks. Omron’s condition monitoring devices support maintenance automation via retrofit installation anytime.

Education
Skill transfer is vital for a company’s capability. Omron’s condition monitoring devices facilitate efficient technical training by digitally replicating skilled engineers’ expertise.

Trust
Production and delivery delays resulting from production line stoppages, accidents, or disasters like fires and gas leaks erode trust within the community. Omron’s continuous remote monitoring via condition monitoring devices enables early anomaly detection.
Omron’s Condition Monitoring Devices Introducing Predictive Maintenance in three steps:
Step 1: “Easily” select the target of monitoring from application examples
Efficiency in creating a sizable system involves avoiding excessive sensor installations, which are costly and labor-intensive. Start by setting priorities and narrowing monitoring targets for effectiveness. Omron’s website provides application examples for easy target selection.
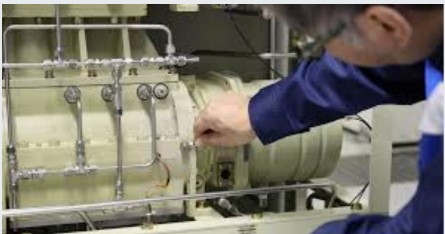
Step 2: “Easily” install the dedicated sensor to the existing equipment
Groups of on-site retrofittable sensors



Step 3: “Easily” visualize using the dedicated tool
The component analyzes collected data with a proprietary algorithm and transmits results to a PC. A dedicated monitoring tool can establish a straightforward 24/7 equipment condition monitoring system, whether on-site or remote.
Automatic analysis of collected data by edge computing (within the condition monitoring device)

Evolution of Omron’s Condition Monitoring Device for a Sustainable Manufacturing Industry
Today: Small start of predictive maintenance in a specific application

Tomorrow: Continuously create added value by using the time created
Incorporating predictive maintenance across the entire factory, utilizing technologies like DX and AI, minimizes maintenance tasks. This enables more time for value-generating improvement activities, supporting sustainable manufacturing.
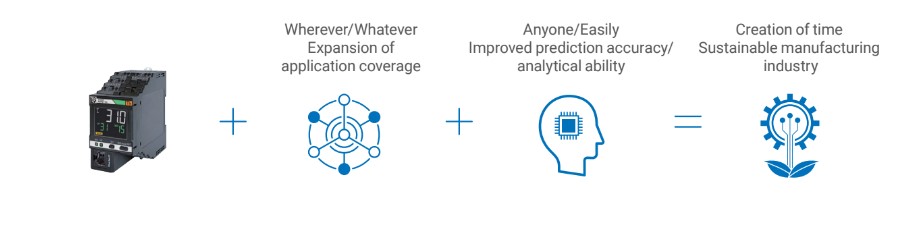
Examples of Introduction of Predictive Maintenance
Since 2017, Omron has launched additional condition monitoring devices, serving over 1700 companies and fostering maintenance innovation. Here are examples detailing the background, introduction process, decision-making, and outcomes of their implementation.
Automobile Industry
Predictive maintenance against heat leak accidents due to cracks in the paint drying process air duct
Background of the issue:
In 2017, Omron introduced its first condition monitoring device, expanding its product range, and serving over 1700 companies to drive maintenance innovation. Amid increasing automation, on-site anomaly detection became challenging in areas without on-site personnel. A heat leak from the high-temperature air duct caused process interruptions, posing fire risks. Regular inspection was impractical due to duct placement along the ceiling.
The company sought a permanently installable condition monitoring device for 24/7 monitoring to enhance maintenance efficiency and reduce fire hazards.
Introduction Process
They first installed a condition monitoring device on one piece of operational equipment to confirm its effectiveness. This success led to its adoption in multiple factories. As each factory conducted its evaluation, the decision emerged to integrate it as a remote monitoring system in a new factory under construction. As part of their IoT implementation, they introduced a predictive maintenance system using Omron’s condition monitoring device. Their plan is to gradually implement it on existing equipment in other factories while assessing its efficacy.
Effectiveness/Evaluation criteria
The company began implementing IoT within its budget for the new factory, allowing for easy future expansion. If condition monitoring proves effective, they will secure additional funds as required for further installations.

Extra Value
Fire incidents can result in supply disruptions, harm the corporate brand image tied to governance, and affect trust with neighbors, consumers, and subcontractors. Therefore, introducing condition monitoring is essential.
Food Industry
Predictive maintenance against quality deterioration due to wear of the packing inside the homogenizer
Background of the issue:
Ensuring product quality requires a homogenizer for mixing fatty and liquid components. Anomalies like packing deterioration, impacting quality, have remained undetectable. Consequently, the company conducts periodic maintenance but seeks a predictive maintenance solution due to quality risks and rising maintenance costs, aiming to quantitatively identify condition changes.

Introduction Process
In response to a company-wide quality issue, a cross-organizational IoT team examined predictive maintenance solutions. They deployed Omron’s solution to every factory due to its perceived potential. As production site staff faced labor shortages and engaged in preventive maintenance, they quickly implemented Omron’s predictive maintenance solution through retrofitting, enabling straightforward verification of its effectiveness.
Effectiveness/Evaluation Criteria
Omron’s solution choice relied on three factors: the capability to visualize packing deterioration in the homogenizer, on-site edge-level management, and economical operation over preventive maintenance costs.

Extra Value
In the food industry, ensuring food quality not only assures consumer safety but also enhances a company’s brand image.
Digital Industry
Predictive maintenance against quality deterioration due to exhaust gas treatment device wear
Background of the Issue:
The company was looking for a remote predictive maintenance solution to implement a smart factory capable of dealing with the ever worsening labor
shortage. They focused on the exhaust gas treatment device (scrubber) since according to their past quality trouble experience, it was the most important piece of equipment managed. They studied signs of failure of the cooling water circulation pump and air conditioning fan system which have great impact on production. They also looked for a solution that could be deployed to other pieces of equipment.
Introduction Process
The company quickly validated its effectiveness by enabling on-site maintenance personnel to initiate condition monitoring through sensor installation and power activation. Typically, implementing predictive maintenance necessitates designing anomaly detection algorithms. Omron’s comprehensive on-site solution also lightened the workload for the new factory system integrator (SI).
Effectiveness/Evaluation Criteria
Key considerations in choosing Omron’s solution included its verification efficiency through retrofit installation and the ease of future expansion. Additionally, it offers on-site capabilities replicating skilled maintenance engineers’ practices.
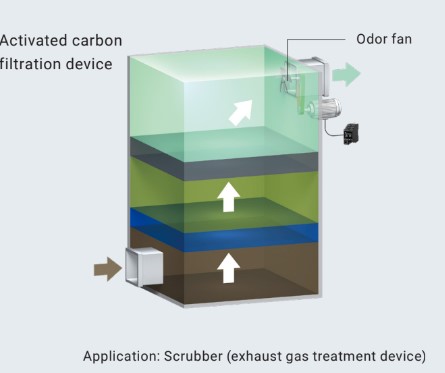
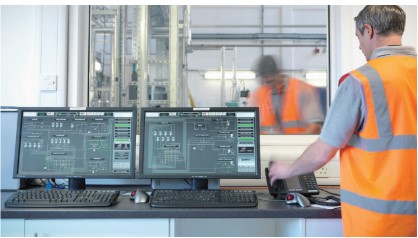
Extra Value
Avoiding unexpected production line stoppage and complying with the supply responsibility enabled the company to increase the trust of users and consumers.
Digital Industry
Predictive maintenance against unexpected stoppage in automated transport system
Background of the issue
An unplanned halt in an automated semiconductor transport system causes substantial losses, including production delays and delivery issues. Initially, to address system overheating concerns, periodic temperature checks were introduced as a temporary fix. However, the risk of unexpected stoppages persisted, particularly in the clean room where inspections were time-consuming and infrequent. They sought a dependable solution for continuous, comprehensive 24/7 monitoring of a wide area to eliminate any oversights.
Introduction Process
The facility design group initiated a project to investigate Omron’s solution. They simulated a real anomaly to assess the time it takes from receiving an alarm via the condition monitoring device to maintenance personnel arriving at the site. Through the assessment, they verified the device’s accurate detection and timely preventive measures. The findings were also shared with other factories for potential implementation.
Effectiveness/Evaluation criteria
The customer evaluated multiple solutions, assessing capital investment, data analyst training, and the risk of missed detection. They chose Omron’s solution due to its potential for rapid evolution into sustainable maintenance activities, considering its ease of study and predictive maintenance system development.


Extra Value
Historically, maintenance relied on human expertise and intuition to identify abnormal conditions. Yet, Omron’s solution offers valuable benefits, enabling skills and know-how transfer. With Omron’s algorithm, anyone who comprehends it can analyze and make consistent judgments.
Omron’s Predictive Maintenance Devices



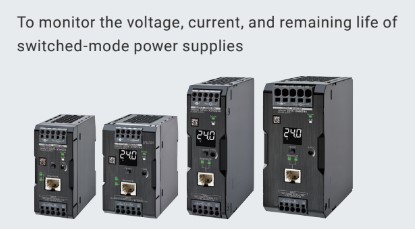