Predictive maintenance is the key to reducing unplanned downtime and operational costs
Amid significant shifts in business conditions, there’s an imperative to reshape the workplace by reducing reliance on skilled maintenance personnel and adopting advanced technology as the primary solution. However, overcoming cost and technological barriers can be challenging. Omron’s approach addresses these challenges by continuously monitoring and analyzing real data through frequent checks.

Remote Monitoring of critical equipment using condition monitoring devices

Resolve issues through condition monitoring
Our predictive maintenance solution replicates skilled maintenance engineer’s analysis, retrofits existing equipment, and enables remote monitoring. This technology simplifies equipment analysis by translating measurement data into alarms, allowing faster issue response by maintenance engineers.

Enables easy implementation of simple and freely scalable remote monitoring systems
Our condition monitoring devices utilize global communication protocols, EtherNet/IP and Modbus TCP, conveying analysis results to higher-level systems. They facilitate versatile solutions for diverse environments, from standalone equipment to entire production lines. We provide essential monitoring tools, analysis software, and PLC connection programs for comprehensive predictive maintenance enhancement.

Replicating the maintenance skills (five senses) of seasoned engineers
Experienced engineers rely on their senses and expertise to detect facility issues, like unusual sounds and movements. At Omron, we develop specialized sensing methods for various applications, incorporating them into our condition monitoring devices.
Retrofit for a quick and easy start
Modifying existing facilities carries risks. Small changes can affect functionality, while large-scale alterations impact production. Omron’s condition monitoring devices can be retrofitted to legacy sites, simplifying predictive maintenance implementation.
Omron’s condition monitoring device features that enable simple remote maintenance
Maintenance innovation driven by remote monitoring systems
From: Do any of the following sound familiar?
- You want to increase patrol inspections but don’t have enough staff
- Responses to sudden facility failures are interrupting other work
- Only a limited group of people can analyze collected data
- The amount of plant data is too massive for comprehensive
management
To: Omron’s simple remote maintenance solutions can help!
- Our systems can reduce risk and resolve staffing issues by replicating the maintenance skills of seasoned engineers through digitization
- Our condition monitoring devices automatically analyze and assess equipment conditions
- Our condition monitoring devices conduct analysis of collected data and escalate the results to higher-level systems in the form of compact high-quality data
- Remote maintenance streamlines operations, freeing up time for more proactive tasks
Analysis and assessment by condition monitoring devices allow for equal levels of visualization on-site and at the office

Edge computing allows for centralization of compact, high-quality data to higher-level systems, enabling streamlined IoT application
From: Massive data collected on-site escalated to higher-level system

To: Condition monitoring devices analyze raw data and escalate only necessary data

Specialized user-friendly tools allow for smooth transition to remote monitoring

Predictive Maintenance Applications
- Remote condition monitoring of hospital infrastructure facilities enables intensive management of chiller pumps and cooling fans
- Remote monitoring of exhaust fans, air conditioning fans, and coolant circulation pumps via SCADA*1 at semiconductor production facility
- Constant remote monitoring for signs of air duct overheating in coating and drying process
- Remote monitoring of voltage/current conditions in overseas manufacturing facilities for early incident resolution
Effect: Significant savings in patrol inspection effort
To enhance the reliability of vital hospital infrastructure, several risk-avoidance measures were implemented, such as frequent inspections. The integration of K6CM, which supports Modbus TCP and EtherNet/IP, into the building management system played a crucial role. This integration facilitated remote monitoring of chiller pumps and cooling fans, focusing on vibration and temperatures. Consequently, it reduced the need for physical inspections, enabling early anomaly detection for systematic maintenance. Moreover, the updated system promotes energy efficiency, preventing excessive energy consumption in deteriorating facilities.
From: Patrol inspections cannot detect degradations in time
People actually had to go to the site for inspections, which was very effort-consuming.
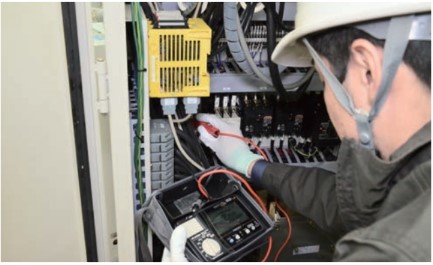
To: Constant monitoring by building management system enables systematic maintenance
Workers can remotely monitor pumps and fans from an intensive monitoring chamber, enabling early anomaly detection and systematic facility maintenance or replacement.

Customer Feedback

K6CM motor condition monitoring device
Effect: High-accuracy condition monitoring enabled by synchronization of monitoring data and other measurement data
Previously, daily on-site inspections were conducted, but they occasionally missed anomalies, resulting in facility failures and operational disruptions. To address this, an automatic monitoring system was implemented in a new building. It primarily monitors critical facilities affecting product quality, such as exhaust fans, coolant pumps, and air conditioning units. However, distinguishing true anomalies from fluctuations in vibration indicators and current waveforms caused by operational changes can be challenging through motor condition monitoring alone. To overcome this, connecting K6CM to SCADA software facilitates synchronization of monitoring data with other measurements. Consequently, this synchronization visually presents results, aiding users in accurately interpreting sensor data and identifying degradation trends.

From: Multiple measurement data could not be viewed simultaneously, making it difficult to distinguish between normal and abnormal operation
Patrol inspection data was segregated by facility, hindering correlation analysis and anomaly detection, elevating the risk of unexpected stoppages.
To: K6CM connected to SCADA software to clarify correlation between data and facility operation conditions
Motor condition monitoring data from specific time points allows for trend monitoring. Analyzing the correlation between this data and information from various facilities facilitates accurate data analysis and enables timely maintenance.
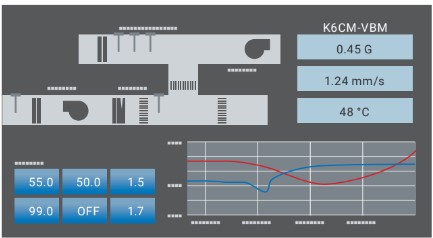
Customer Feedback

Thermal condition monitoring device (K6PM-TH)
Effect: Better worker safety, reduced risk of hot air leaks
Coating and drying processes in car manufacturing pose significant risks. In the drying oven, air at 400°C travels through air ducts for drying. These ducts degrade over time, potentially causing leaks of air hotter than 100°C, leading to burn injuries during inspections. Hot air can also overheat coating components, halting production and risking human harm. The air ducts wind through inaccessible spaces, complicating inspections. Aside from safety concerns, optimizing workflow in coating line maintenance is crucial.
From: Dangerous sites must be inspected in person despite accident risks
Hot air leaks from air ducts pose a risk of burns and injuries during on-site inspections. Additionally, these leaks are unpredictable and may not be detected in routine inspections conducted only a few times a year, causing delays in taking prompt action.
To: Remote monitoring eliminates the need for dangerous inspections
K6PM remotely monitors temperatures around air ducts, enabling users to detect hot air leaks in office environments. This reduces the need for hazardous patrol inspections and facilitates early intervention for overheating issues.
Customer Feedback

Effect: Data from overseas plant sites can be analyzed at mother plant, enabling remote support for failure recovery
The growth of digital device and electric vehicle markets drives demand for electronic parts in camera control. Increased production emphasizes the importance of reducing takt time and defect rates, which experienced engineers continuously address. However, new overseas production plants face challenges as inexperienced maintenance workers struggle to identify and resolve issues. Travel restrictions due to the COVID-19 pandemic limit veteran workers’ support. To address this, the customer needed a remote assistance system. As a first step, they developed a monitoring system utilizing S8VK-X to track power supply voltage and current conditions, critical for equipment operation.

From: Inexperienced maintenance workers cannot quickly resolve issues on their own
Time and quality were under management, no data was collected to investigate incident causes, including current or voltage changes. Consequently, the time needed for failure recovery fluctuated based on the worker’s experience level.
To: Constant monitoring of current/voltage conditions and data collection allow skilled engineers to provide remote support for recovery
A system for monitoring voltage and current conditions enables skilled engineers to offer remote incident support to on-site workers. Additionally, the collected data facilitates straightforward maintenance planning.
Customer Feedback

Insulation resistance monitoring device K7GE
Recognizing insulation resistance trends is vital for averting facility downtime and electrocution risks. Yet, the shortage of experienced maintenance staff poses a challenge in conducting manual measurements. Unlike previous systems that required onsite measurements, K7GE employs the same principle as insulation resistance meters, facilitating automated measurements through trigger signal input, streamlining maintenance practices.
Measurements can be made more frequently for accurate identification of the slightest facility anomalies
Measuring insulation resistance in a facility can have substantial consequences, necessitating power-off and resource allocation. This infrequent measurement approach may lead to unnoticed insulation degradation and sudden downtime. K7GE, however, enables fast and automated insulation resistance measurement, minimizing production disruption, and facilitating frequent assessments.
From: Manual management using megohmmeter
To: Automatic measurement by K7GE
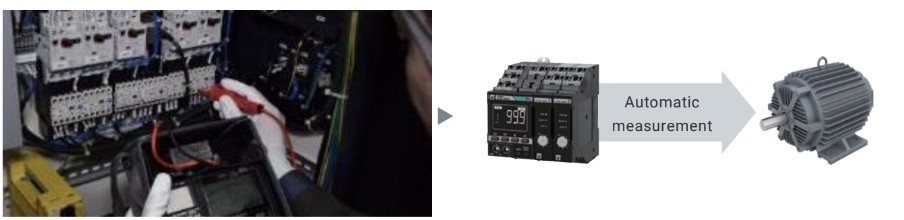

Insulation resistance data collected via communication is visualized in remote locations for systematic maintenance
Measurement results are visible on the K7GE unit on-site and can also be remotely monitored at office locations through touch panel screens. This is achieved by connecting the unit to PLCs via network communication using interface converters.

Application Examples
Monitoring insulation degradation of metal parts processing machine
NC machine tools and machining centers utilize cutting oil for metal processing, but this oil can vaporize and infiltrate built-in motors, hastening insulation degradation. Regular insulation resistance checks are challenging since motors inside the facility necessitate production downtime. However, K7GE simplifies this by automatically measuring when the facility powers off, facilitating more effective degradation trend monitoring. Additionally, up to eight probe units can be installed, enabling monitoring of processing machines with multi-axis motor control systems.
Monitoring insulation degradation of exhaust fans for coating process
During the coating process, exhaust fans draw in air with vaporized coating material, potentially causing insulation degradation within the fans. Facilities requiring insulation resistance measurement are often situated at elevated locations, posing safety risks to workers. K7GE enables automated and secure measurements, enhancing efficiency and safety.
Maintenance tips
Power Supplies
Issue: Facilities that were operating normally yesterday are not starting this morning when powered on. Investigation revealed that 24 VDC power is not being supplied from the power supply.
Cause: The power supply may have reached its end of life due to electrolytic capacitor degradation.
Power supplies naturally age and should be regularly replaced. Over time, their electrolytic capacitors deteriorate, affecting performance, especially in starting under low temperatures. This issue worsens as capacitors degrade, ultimately leading to failure. When a power supply’s electrolytic capacitor significantly degrades and cools during power-off periods, it may fail to start. Other problems caused by capacitor degradation include reduced power output and increased ripple noise. For instance, a 24 VDC power supply may drop to about 22 VDC or exhibit voltage fluctuations due to capacitor deterioration. These symptoms, although subtle, signal the product’s approaching end of life but can be easily overlooked, especially when operating 24 VDC devices.
Solution: You can reduce the risk of unexpected stoppage by using power supplies that can visualize when they should be replaced.
Omron offers a feature that continuously calculates electrolytic capacitor degradation in our power supplies based on usage conditions like ambient temperature and load factor. This calculation result is presented as a percentage of the remaining time (in years) before replacement. It starts at 100% upon shipment and decreases in 0.1% increments, providing users with a reference for deciding when to replace their power supply.

Temperature controller and related equipment
Issue: Peripheral devices in temperature control often encounter issues in packaging machines and similar equipment with moving heaters. Replacing these devices doesn’t resolve the problem, as the replacements also fail shortly after installation.
Cause: The devices being used may not be equipped to withstand the operating conditions.
Temperature control involves a system of controllers, thermocouples for measurement, and heaters, often in machines like packaging equipment. Issues in temperature control commonly arise from peripheral device problems like burnouts, disconnections, or short circuits due to mechanical or thermal factors. Extending system life necessitates understanding its operation and replacing peripherals with more durable options. The chart below offers functional details on key components and proactive measures for longevity.
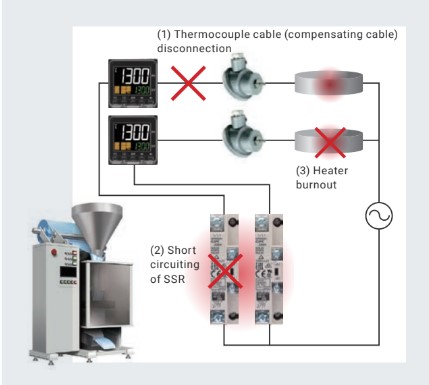
Solution: Reduce failure incidents by mitigating equipment degradation and preventing rapid heating.
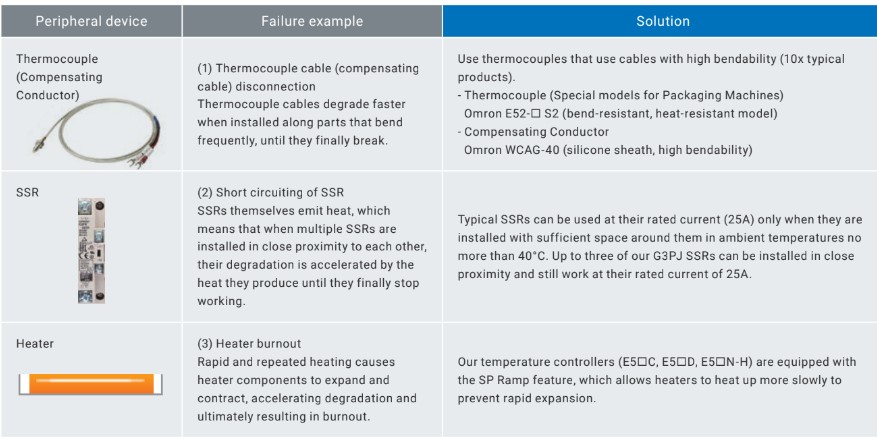
Omron’s Predictive Maintenance Solutions