Connectivity & Interoperability (Part 3) – Enabling Interoperability with OPC-UA
Enabling Interoperability
Interoperability can be defined as; the ability of two or more products, programs, or systems, to exchange and interpret each other’s data. Ability, in this sense, can refer to both the means to interact and the quality of that interaction. Connectivity allows the conversation to take place between these elements; interoperability ensures they speak the same language.
The factory, and the wider manufacturing supply chain, has evolved through successive industrial eras into an incredibly diverse technology landscape. Every production facility is made up of a plethora of equipment, of different ages, from numerous manufacturers, and with varying approaches to communication.
Industry 4.0 wants to connect all those “things” and more, but only if they can talk to one another. To bring about the vast benefits of a smart connected factory, manufacturing operations will need to enable a high level of interoperability.
Interoperability has become a key challenge for the development of Industry 4.0 technologies. The sector has been slow to create and agree upon adequate standards for secure exchange of data between machines, devices, and services across different companies and industries, leaving us with a somewhat fragmented interoperability landscape.
However, as we move into a new decade there is optimism about the increasing collaboration within the industry and the interoperability standards that are currently establishing themselves in the manufacturing space.
Interoperability Standards
The whole Industry 4.0 initiative focuses on connecting IT and automation in a strategic way, thus forcing interoperability technologies such as Open Platform Communications Unified Architecture (OPC UA) in the spotlight. Industry 4.0 and related initiatives accept that open software and communications standards are vital to self-managing production processes.
In order to drive the Industrial movement and bring about the economic growth it promises, standards are essential to enable controllers, sensors, equipment, machines, humans, and other systems to cooperate and communicate directly.
Design engineers of Industry 4.0 demonstration processes acknowledge this need by using existing standards, such as the ISA95 integration standards in their designs. Adopting these standards recognises that manufacturing processes are filled with international interdependencies, which require shared standards and interoperable technologies. Hence, Singapore Smart Industry Readiness Index (SIRI) encourages companies to standardise or make use of complementary communication technologies and protocols to establish more open, inclusive, and transparent communications networks.
Three standards have emerged as the most important building blocks of Industry 4.0 interoperability, each with its own history, best use cases, and capabilities within the manufacturing supply chain. Critically, these standards are platform independent, which enable devices sold by different vendors to exchange information without system hang-ups.
OPC UA - the New Standard for Industry 4.0 Connectivity
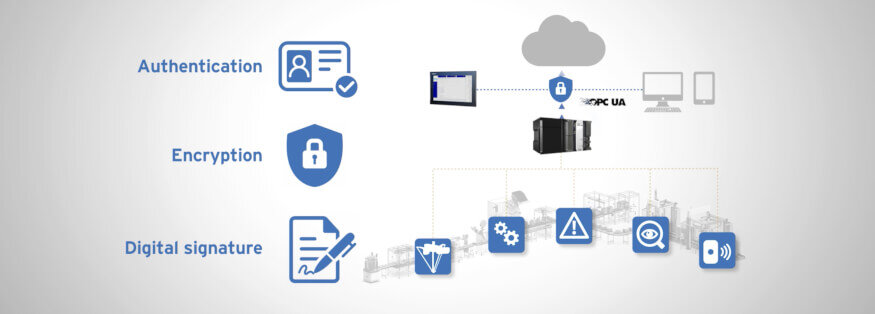
Open Platform Communications (OPC) is the prominent interoperability standard, and a vital element in digital manufacturing and automation efforts. OPC is an interoperability standard used to secure the exchange of manufacturing automation data.
Early versions of OPC (or OPC Classic) —OLE for Process Control— were plagued by security problems, closed architectures, maintenance difficulties, and time-consuming data management. Its complexity and expense made it difficult to run and unsuitable for use in Industry 4.0 applications. Early Industry 4.0 adopters would need a standard that enables improved functionality and usability, OPC responded with the significant Industry 4.0 improvements built into the updated version — the OPC UA standard.
Key Features of OPC-UA
- Machine-to-Business — OPC-UA is the first communication technology built specifically to run in the grey zone, where data must cross firewalls, security barriers, and specialised platforms to make that all-important, machine-to-business connection.
- Efficient Data Handling — OPC-UA provides a very flexible and adaptable way to move data between enterprise IT systems and the controls, sensors, and monitoring devices that handle real-world data.
- Tool Utilisation — The OPC-UA protocol connects analytic tools, databases, enterprise resource planning (ERP) software, and other IT solutions to real-world data collected from low-end controllers, sensors, actuators, and monitoring devices.
- Backward-Compatible — Based on extensible SOA(Service Oriented Architecture) framework the OPC-UA is backward-compatible with OPC and uses a software design approach that has become widely used in manufacturing systems around the world.
- Platform Availability — OPC-UA supports a wide range of platforms, from embedded microcontrollers to cloud infrastructure for greatest integration flexibility.
- Enhanced Security — The OPC-UA standard provides high levels of security through encryption, authentication, and auditing.
Based on the statement of OPC Foundation, the vision of IoT can only be realised, if the underlying communication between central components is based on a global communication standard that can fulfil a wide range of complex requirements. Thus, using a common standard makes a lot more sense to preserve the value of overall datasets.
OPC-UA ensures the open connectivity, interoperability, security, and reliability of industrial automation devices and systems. Currently, OPC-UA has become the main communication and data modelling standard for Industry 4.0. It’s completely scalable, works with many software platforms, and its widespread adoption is quickly making OPC-UA the backbone of Industry 4.0 connectivity.
Getting Connected to Industry 4.0
The wealth of benefits and its futuristic aura has led many small- and medium- sized manufacturers to believe that Industry 4.0 is an expensive endeavour reserved for the major players. This is not the case, however. Industry 4.0 technologies and systems are inherently scalable, designed to grow with companies. Most applications are focused on cost-savings and increased productivity, allowing firms to do more with less and promising fast ROI.
ASEAN focused research suggests a gradually growing awareness in the region that a “low-and-slow” approach to Industry 4.0 can suit companies of all sizes, although trade media paints a picture of shiney, 100% digital, highly-connected, fully-automated factories.
The truth is that Industry 4.0 is increasingly being used to supercharge legacy equipment and established operations, application by application according to needs and budgets. All enabled through connectivity and interoperability.
Those looking to begin their path to Industry 4.0 slowly have a wide variety of options to suit their unique situation. There are opportunities to connect existing and new manufacturing technology, for example. Even old machinery can be connected to monitoring software indirectly with a simple sensor, albeit with a minor loss of accuracy. These can provide initial AI and automation applications, which can be built upon gradually as the benefits are demonstrated and the overriding strategy develops.
Paul Miller, senior analyst at Forrester addressed that a lot of industrial machines have been putting out some sort of electronic signal, but connecting it with the modern analytical platforms is certainly a tough job to do,”. He suggests manufacturers set right expectation on the Improvement that single step can provide, and a smart factory can simply be a prototype sensors measuring things since all that really matters is that the factory technology connects.
Simple 4-Step Strategy for Industry 4.0 Connectivity
Consider this simple 4-step strategy for a manufacturer to launch their Industry 4.0 ambitions:
- Upgrade to OPC-UA IIoT architectures.
- Tie the architecture into an existing factory automation infrastructure.
- Feed factory data to the latest cloud-based advanced analytic tools.
- Use data analytics and visualisation tools to monitor and optimise processes in line with company goals.
With the right guidance, digital transformation doesn’t need to be a stressful and disruptive process. As always with technological transformations, early adopters take the risk to earn substantial rewards.
In Industry 4.0, however, the scalability of connectivity allows manufacturers to “test the water” with a range of approaches to suit their needs. So they can understand what Industry 4.0 can do for them before they decide how to revolutionise their business.
Vidya Ramnath, Vice President, Global Plantweb Solutions & Services, Emerson Automation Solutions, states that one of the key disruptive forces of Industry 4.0 is the ever-increasing volume, velocity and value of data. Looking ahead, traditional manufacturing companies need to change their perception of data, not just as numbers on a screen, but as a strategic asset that can unlock revenue growth and deliver cost savings. Companies who embrace this shift will start building the infrastructure for connectivity and intelligence right away.
Written by Colin Koh, Senior Business Development Manager, Industry 4.0 Consultant. This Industry 4.0 Article Series is aimed to enlightened readers about everything they need to know about Industry 4.0 and its application about technologies and benefits to companies and consumers.
Industry 4.0 Portal Articles
- What is Industry 4.0 And How It Began (Part 1) (Part 2) (Part 3)
- The Industry 4.0 Framework: Idea, Tool, & Guide (Part 1) (Part 2)
- The Smart Factory – 6 Key Principles You Should Achieve
- The Smart Factory- All You Need to Know About The Requirements
- Connectivity & Interoperability (Part 1) (Part 2) (Part 3)
Need help on your i.4.0 journey? Drop us an enquiry below.
MORE INTERESTING ARTICLES
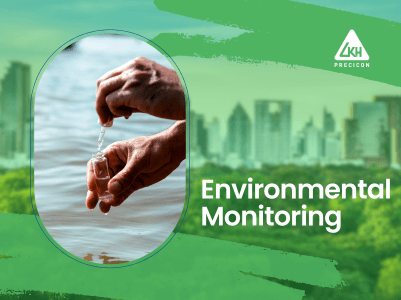
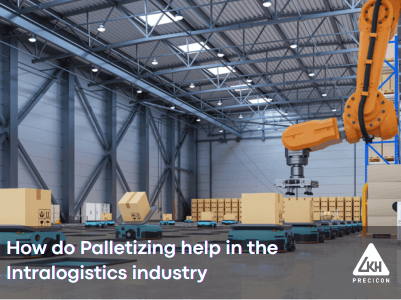