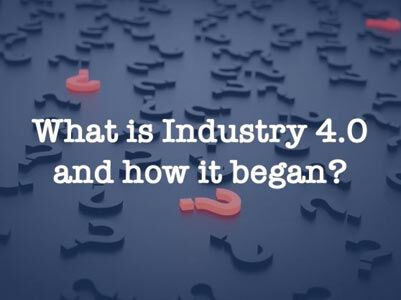
What is Industry 4.0 and how it began
Waiting for Industry 4.0
What is Industry 4.0? Walk onto the assembly floor of the VinFast car assembly plant in Hai Phong, Vietnam, and immediately, you notice that this is not a traditional manufacturing operation. The general atmosphere is one of quiet, coordinated motion. Yes, you hear the whine of power tools, but mainly, you notice the orderly stacks of parts and the coordinated movement of humans and machines — 1,200 Swiss-made robots from renowned manufacturer…
Many of the sights and sounds you experience are the results of manufacturing inventions, processes, and ideas developed during the past 270 years. The history of manufacturing technology is filled with useful knowledge and social incentives. These drivers led to changes in technology and practices in three industrial revolutions. Now, companies and governments consider the requirements and potential outcomes of a fourth industrial revolution, also known as Industry 4.0.
Retracing connections between past ideas, incentives, and production capabilities is a useful way to assess business and social challenges we are likely to face in Industry 4.0. So, our modus operandi will be to consider the big ideas, useful knowledge, and incentives of each industrial revolution. Then, we’ll see which practices and capabilities emerged from the changes made.
“The Industrial Revolution was another of those extraordinary jumps forward in the story of civilization.”
Stephen Gardiner
Industry 1.0: Power & Productivity
When we say, “the Industrial Revolution,” what do we mean? There are many definitions, which go something like this one: “The era of economic and social changes, which began with the mechanisation of agriculture and manufacturing, at about 1760 in England and later in other countries.”
Given our society’s focus on technological progress, it might be helpful to change the importance a bit. By moving our attention from the period to the role of change, our description of Industry 1.0 becomes: “The era from 1760 to 1830, represented by steam-powered, factory-based production, in which profound economic and social change became the normal condition.”
School Books encourage us to think about the Industrial Revolution, a single-stage event that changed society in one go, but this is not so.
Measuring Time by Technological Change
Historians of technology now recognise not one but three past industrial revolutions. These society-changing surges of technological development (revolutions) are separated by lulls in innovations (evolutions). In evolutionary periods, technological developments are improved little by little and absorbed into standard manufacturing methods.
Where are we today? — Using this model of time and change, modern industrial progress spans 270 years of social, economic, and technological change. Not all historians agree where we are along the industrial revolution timeline. Most consider that in 2020, which we’re edging into the fourth industrial revolution (4IR) or Industry 4.0.
Some societies still run their manufacturing businesses with technologies, methods, and ideas typical of Industry 1.0 through 3.0. However, in later chapters, playing technological catch up is an important part of achieving the full value potential that Industry 4.0 offers.
Progress as technological surpass each surge in manufacturing development is enabled and expanded by innovations of earlier stages. Our walk through the VinFast plant provides glimpses of artefacts from previous revolutions as well as current times: machined car parts (Industry 1.0), assembly lines and electrical power (Industry 2.0), and electronic production controls and robots (Industry 3.0).
Centralising, Mechanising, & Powering Work
In 1760s Great Britain, manufacturing innovators became aware of the business opportunities enabled by two factors of production: a denser-than-water power source and the then-new notion of factory production.
There was no single “aha!” moment in this development. Inventors and investors gradually realised that businesses could fill the growing demand for manufactured goods. To reap the financial benefits, they had to do three things:
Gather all production resources at one centralised location, the factory, rather than in scattered places at workers’ homes.
- Substitute human and water energy with coal-based steam power.
- Speed up the manufacturing process by using special-purpose, machinery rather than human effort.
The result was goods that could be manufactured at an unprecedented speed and scale. For the first time, observers noticed physical improvements in the lives of a single generation of industrial workers
The development of useful knowledge — it’s easy to think about the first industrial revolution as being invented without the basis of prior knowledge and experience. The truth is, mid-eighteenth-century British society was already technologically competent. Mechanisation was also well underway in Britain’s agricultural sector.
As early as the late 1700s, British society had its engineers, mechanics, millwrights, and tinkerers. They all made things —and kept them operating — with their hands, skills and collective experience. They called this “useful knowledge” and made it a pillar of economic and social progress.
This knowledge didn’t explain scientific theory (although there was always a strong connection between scientists and engineers during this period). Instead, it focused on practice, combining the skills of the artisan with technical knowledge and specific skills needed to design, make and operate machines.
A foundation of technological and financial infrastructure — That close connection between the builders, engineers, and scientists developed within important technology hubs. Located at south Lancashire, southwest Scotland, Birmingham, and the West Midlands, these cities and regions became centres of invention and investment. Banks were slow to fund new farm technology ventures. However, merchants, projectors (people who planned and set up projects or enterprises), and speculators picked up the slack.
Early Incentives of Machine Development
The urge to develop industrial machines grew with the increasing demand for consumer products. The gradual and growing understanding of the role of machines in improving manufacturing productivity was another stimulus.
From the earliest days of the first industrial revolution, money was on everyone’s mind. Machine designers, makers, and buyers had two questions: “Would it work?” and “Would it make money?”
Potential buyers had to be persuaded that agricultural machines can deliver the productivity and profit they promised. A process that began on British farms decades before the industrial revolution. Gradually the successful development of farm equipment and promise of increased cash flow encouraged forward-looking investors to experiment with new machines and processes.
New Energy Sources & Disruptive Ideas
The combination of a new energy source and a new way to organise work provided the foundation of Industry 1.0. Development of coal-powered steam technology and the creation of the factory system are the most familiar parts of the early Industrial Revolution.
First Industrial Revolution
The knowledge of builders and mechanics through experience of mechanised agriculture, and the formation of investment and technology hubs are lesser known parts of pre-industrialisation. However, these ideas and events were crucial in helping Industry 1.0 change manufacturing and laid the foundation for many innovations to come.
Pre-industrial Conditions in ASEAN Nations
In the 1760s, Britain who started seriously industrialising was quickly followed by other major European economies of the time. Two centuries later the ASEAN bloc was formed, and it was only then that Southeast Asian countries started seriously in industrialisation.
Other than Singapore, manufacturing processes in Southeast Asia at the time were relatively primitive and small-scale. The manufacturing operations were dominated by local natural resource processing. Products included a narrow range of consumer goods sold to domestic markets.
There were a few large modern industrial plants and very little foreign direct investment. Investment activity that existed was a holdover from the colonial era. Manufacturing entrepreneurs in ASEAN nations had to import much of the skills, experience, and funding needed to start local manufacturing sectors.
Industry 1.0 to Industry 4.0 Summary
To continue reading on the this article about Industry 2.0, please click here.
To read about Industry 3.0 & Industry 4.0, please click here.
Written by Colin Koh, Senior Business Development Manager, Industry 4.0 Consultant. This Industry 4.0 Article Series is aimed to enlightened readers about everything they need to know about Industry 4.0 and its application about technologies and benefits to companies and consumers.
Industry 4.0 Portal Articles
- What is Industry 4.0 And How It Began (Part 1) (Part 2) (Part 3)
- The Industry 4.0 Framework: Idea, Tool, & Guide (Part 1) (Part 2)
- The Smart Factory – 6 Key Principles You Should Achieve
- The Smart Factory- All You Need to Know About The Requirements
- Connectivity & Interoperability (Part 1) (Part 2) (Part 3)
Need help on your i.4.0 journey? Drop us an enquiry below!
MORE INTERESTING ARTICLES
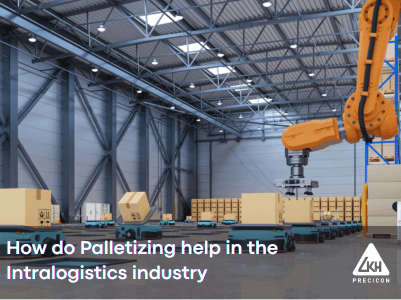
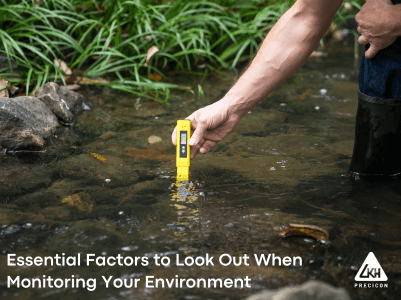