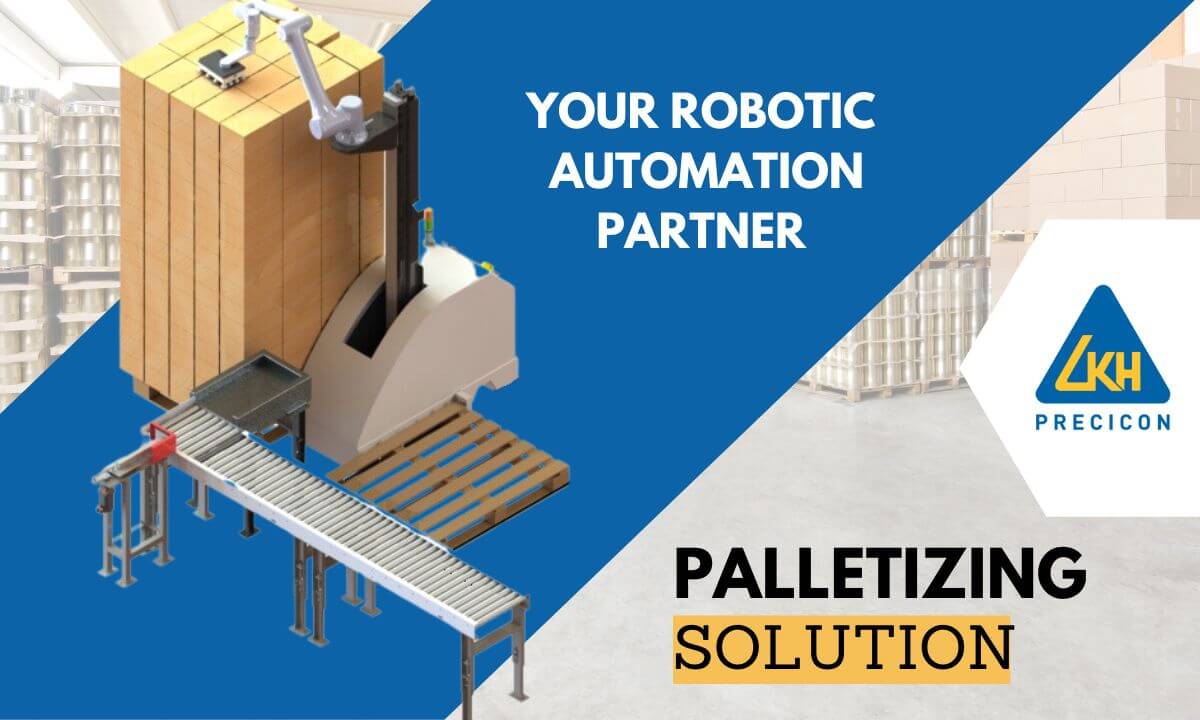
Efficient Palletizing Starts with Us
Palletizing is a tertiary process occurring immediately prior to warehousing and final shipping in the overall process.
There are two system types: centralized and decentralized.
The concept of centralized palletizing entails arranging the factory layout in a manner that consolidates all manufactured goods at a designated location where palletizing is done, typically facilitated by a conveyor system.
(High-volume production environments where large palletizing robots are used to quickly pack hundreds or thousands of products an hour)
Decentralized palletizing involves the distribution of manufactured goods across multiple locations within the factory floor, with each location featuring an independent station dedicated to palletizing.
(Multiple palletizing robots that each only handles one or a few product lines. This allows teams to be responsible for their entire product line, including packaging)
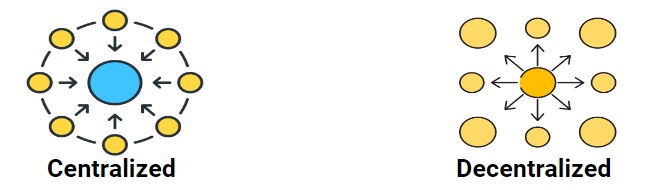
A Comparison for Palletizing
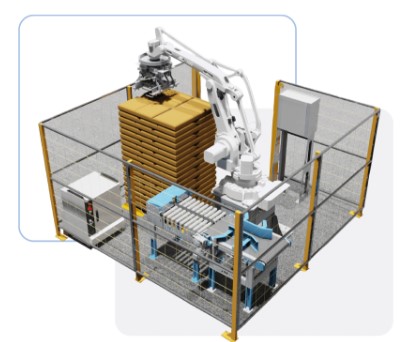
Industrial Robot
Robot types | Industrial Robot | Collaborative Robot |
Speed | Very fast. 10-40 bags per minute or more with layer palletizing | Faster than you might think. Up to 13 cycles per minute |
Payload | High for many systems but varies 5-800kg | 16kg |
Programming | Hard. Requires extensive specialist knowledge | Easy. Anyone can do it with minimal training |
Size | Huge. Requires a lot of floorspace | Small. Just larger than 2 pallets |
Fully loaded cost* | $$$$ | $$ |
Max pallet height | 1-3m | 1.5-2.75m |
Safety requirements | Requires a fence and often extra sensing | Can require some sensing and fencing |
Case of redeployment | Hard, Requires a lot of work to switch to another task | Can use the robot for other tasks if necessary |
Deployment time | Several months | A couple of weeks |
*What is a fully loaded cost? In case you’re not familiar with this term, fully loaded costs include both the direct cost of the robot and the indirect costs associated with the deployment. These indirect costs add a lot to the cost of an industrial robot system.
Automated Palletizer
For decentralized palletization, the process traditionally entailed manual labour involving the placement of goods or materials onto pallets or containers, typically positioned in proximity to conveyor belts for packaging or bulk product discharge, or strategically located in a convenient location to facilitate item acceptance.
Automating Palletizer translate to:
- Not relying on an ageing and possibly shrinking manual workforce. Manual repetitive labour is being shunned by all ages in our society.
- Not shutting down the palletizing system due to employee injury because of back strain. A simple sprain can lead to unexpected long-term medical issues for both the employees themselves and also for company insurance premiums.
- If applicable, reassigning humans to value-added tasks in the organization.
- Employees do not like dull and repetitive steps. Utilize their skills elsewhere. Long-term employees already have a vested interest in company success.
- End product consistency and quality. Intactness of packages and boxes. Satisfied customers as to what they find on their incoming pallets.
Features of Automated Palletization
Different box/item surfaces can be handled | Adapts to all object configurations |
Adapts to product size changes | Easily deployed in as little as a few hours |
Can be redeployed | May fit in smaller spaces |
Quick set-up time | Reduces employee hours at the end of the line |
Reduces employee numbers at the end of the line | Removes human injury at the end of the line |
Removes human repetitive tasks at the end of the line |
User Concerns
The fully loaded cost is a clear differentiator. But both robotic systems can have a good return on investment so this is less important than some of the other differences.
Three important concerns for many users are deployment time, ease of redeployment, and ease of programming. These are what make collaborative robot systems so much more flexible than industrial robots. They are easy to program, deploy, and redeploy.
If you need to process a high volume of products or you are palletizing very heavy objects, an industrial robot may be the best solution. If you want a highly flexible system that is easy to use and quick to deploy, a collaborative robot is probably the best bet.
Hardware Palletizing Robot
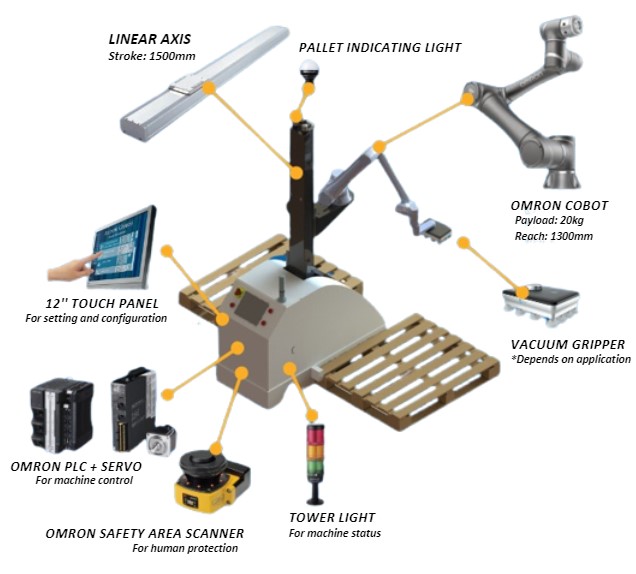
Product Designs
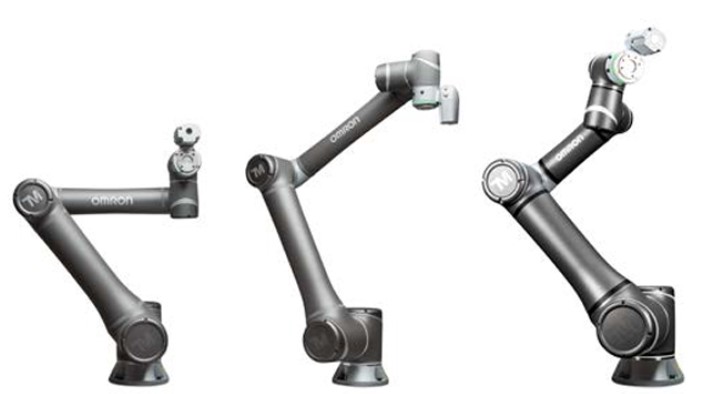
PR12LA
Reach: 1300 mm
Payload: 12kg
PR20LA
Reach: 1300 mm
Payload: 20kg
PR25LA
Reach: 1900 mm
Payload: 25kg
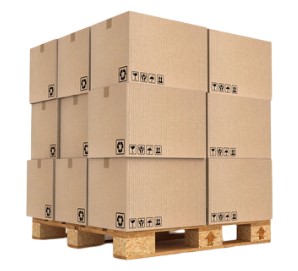
Max Pallet Height:
2200mm
Max Cycle Time:
13 cycle/min
Technical Drawing of Robot
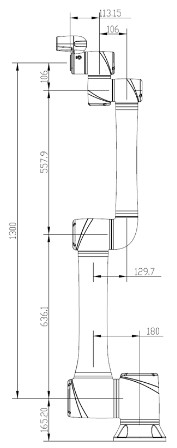
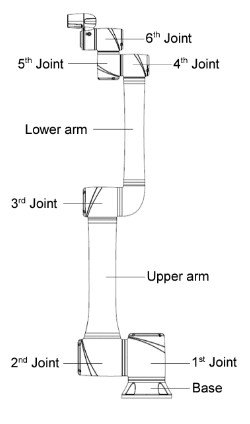
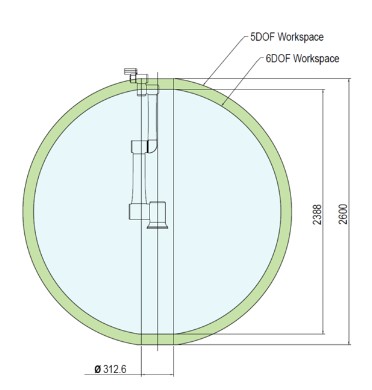
Technical Specifications
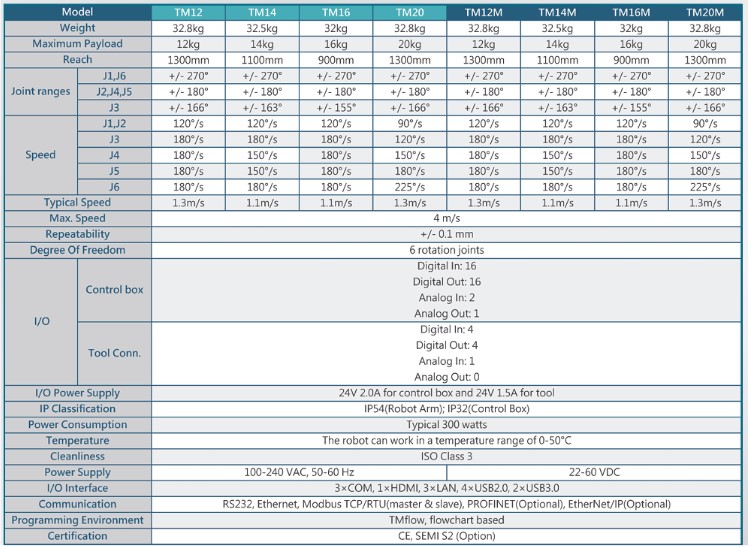
Information Requirements
- Determine the output of the palletizing cell. What is the target pace and production rate? How many pallets can be loaded, and how many boxes or packages can be placed in a given time window?
- Determine the arrangement or configuration of the pallet. This information can come in a variety of formats such as layer pattern, layer sequence, and package layout.
- Determine the weight of boxes and/or packages.
- Determine the floor space required. Palletizers take up more room than a manual labourer. They also cannot move out of the way when lift trucks manoeuvre around the pallet
- Determine the maximum height of the fully loaded pallet.
- Determine the box dimensions
Introducing Palletizing Solution
Interested to find out more about Palletizing Solution? Feel free to contact us!