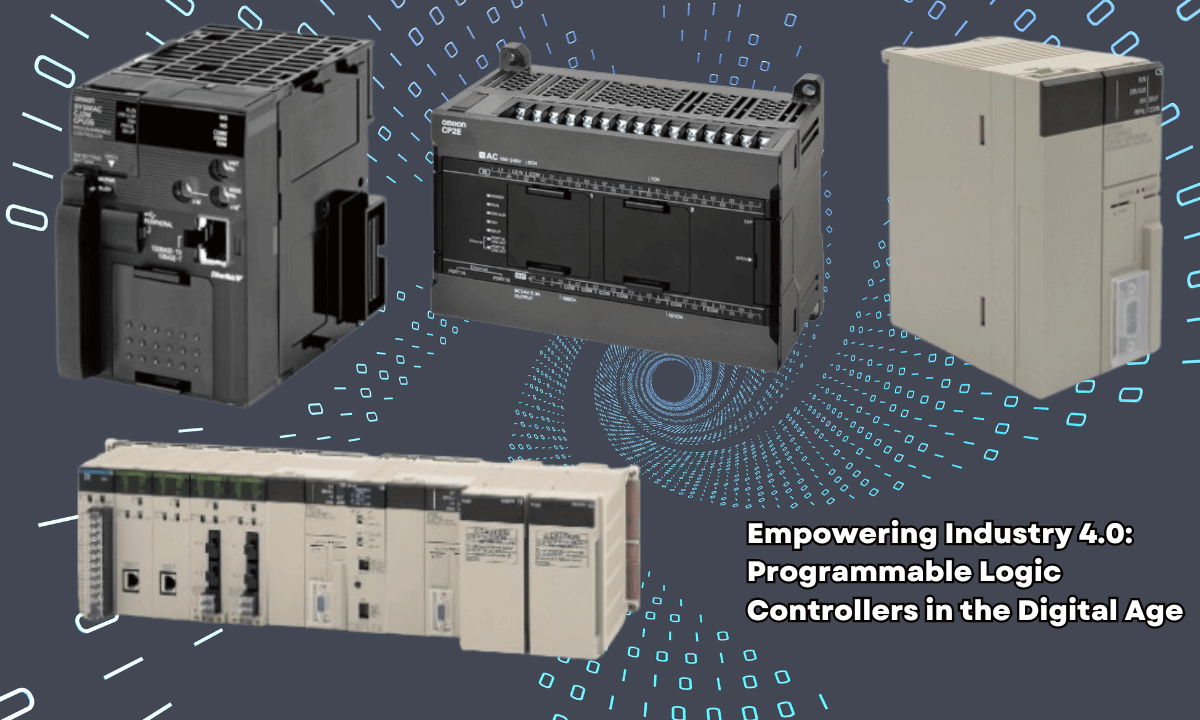
How does Programmable Logic Controllers (PLCs) Operate?
Programmable Logic Controllers (PLCs) are specialized digital computing devices equipped with diverse inputs and outputs. Specifically crafted to manage and automate industrial processes and machinery, PLCs operate by monitoring inputs from sensors such as temperature or pressure devices. They then process this data through a programmed logic sequence, which, in turn, directs output actions to control actuators, motors, or devices. This systematic approach plays a crucial role in optimizing industrial processes for enhanced efficiency and precision.
What Are the Advantages of Using PLCs Over Traditional Relay-Based Control Systems?
PLCs offer a number of advantages over traditional relay-based control systems such as:
Flexibility in programming – PLCs are programmable, allowing users to easily modify and update their control logic by reprogramming. PLCs are programmed using specific languages such as ladder logic, structured text, function block diagrams, sequential function charts, and instruction lists, allowing users to design logic sequences to manage and optimize a wide range of industrial processes. In contrast, users cannot reprogram relay-based systems, requiring physical wiring for any alterations.
Ease of Troubleshooting – PLCs provide detailed diagnostic capabilities and error reporting, simplifying the identification and resolution of issues. Troubleshooting in relay-based systems is more complicated in terms of wiring and typically involves manually inspecting each relay and connection point.
Faster Response Times – PLCs are capable of responding to inputs and producing outputs much faster than traditional relay-based systems. Traditional relay systems have longer reaction times due to the mechanical nature of relays.
Integration with Digital Systems – PLCs can integrate with digital systems through various interfaces and communication protocols. They can communicate with sensors, actuators, Human-Machine Interfaces (HMIs), and other control devices. Relay-based systems lack this digital integration capability.
What are some common applications of PLCs?
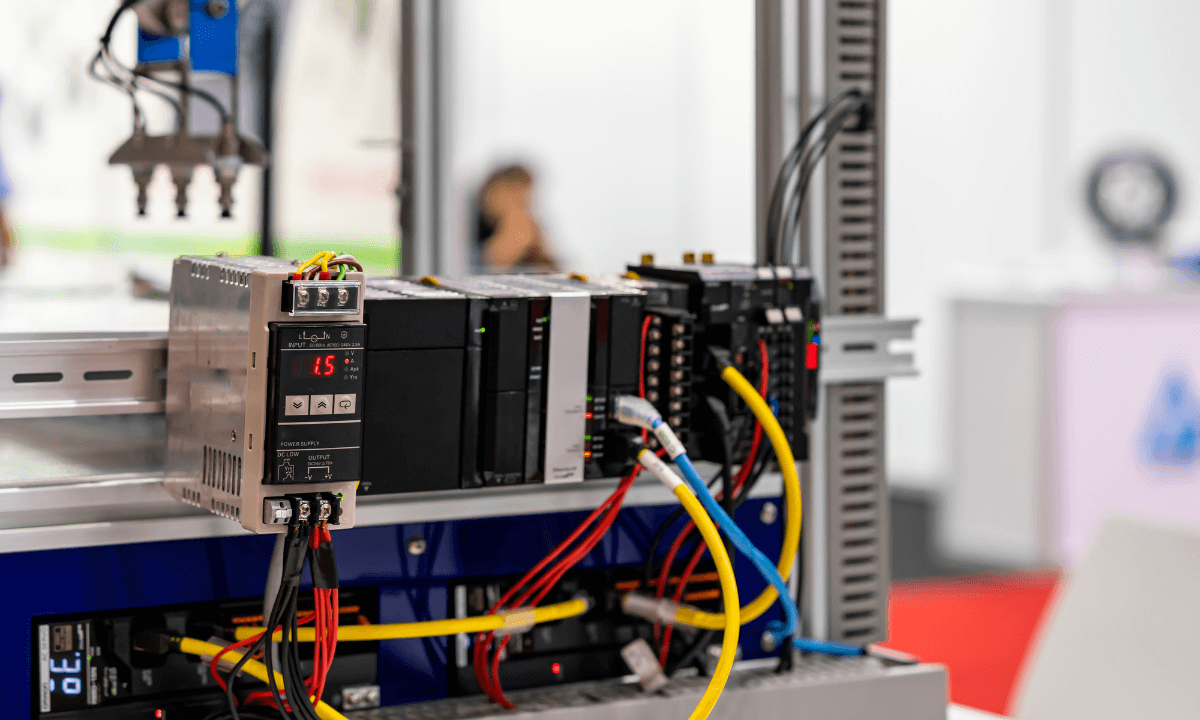
Manufacturing & Factory Automation – PLCs play a crucial role in controlling and automating manufacturing operations, including assembly lines, conveyor belts, packing machines, material handling, and robotics. They optimize production, enhance efficiency, and ensure consistent quality in factories.
Automotive Industry – PLCs are vital in automotive assembly lines, overseeing robotic arms, conveyors, welding machines, and more. They enhance production flow and ensure precision in car manufacturing.
Power Generation and Distribution – PLCs control generators, switchgear, and substations in power plants and distribution networks, facilitating the monitoring and management of electrical characteristics and ensuring seamless electricity distribution.
What Roles do PLCs Play in the Context of Industry 4.0?
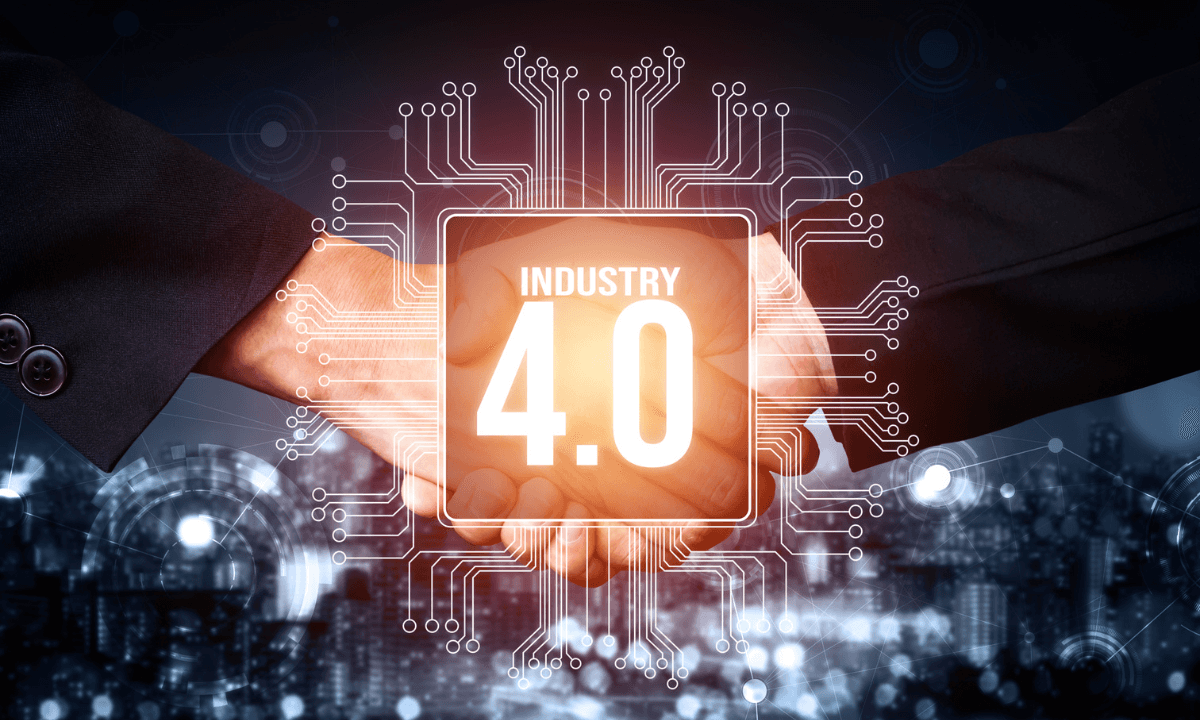
In the context of industry 4.0, PLCs play a crucial role in revolutionizing industries to become efficient, flexible and autonomous. Serving as a vital link in smart factories, PLCs enable seamless communication and collaboration among various devices and machines. Their real-time data acquisition and analysis capabilities support predictive maintenance and operational optimization.
PLCs’ integration with Internet of Things (IoT) devices enhances overall visibility and control, thereby supporting informed decision-making. Moreover, PLCs promote human-machine collaboration through advanced Human-Machine Interfaces (HMIs), consequently improving productivity and reducing the need for manual intervention.
Beyond these roles, PLCs ensure reliability in controlling machinery, reducing downtime and maintenance costs. Their rugged design allows them to withstand harsh industrial conditions, making them indispensable for uninterrupted critical processes.
Overall, PLCs play a vital role in establishing manufacturing environments that are efficient, secure, and adaptive, aligning seamlessly with the objectives of Industry 4.0.
What Emerging Trends or Technological Advancements are Shaping the Future of PLC Technology?
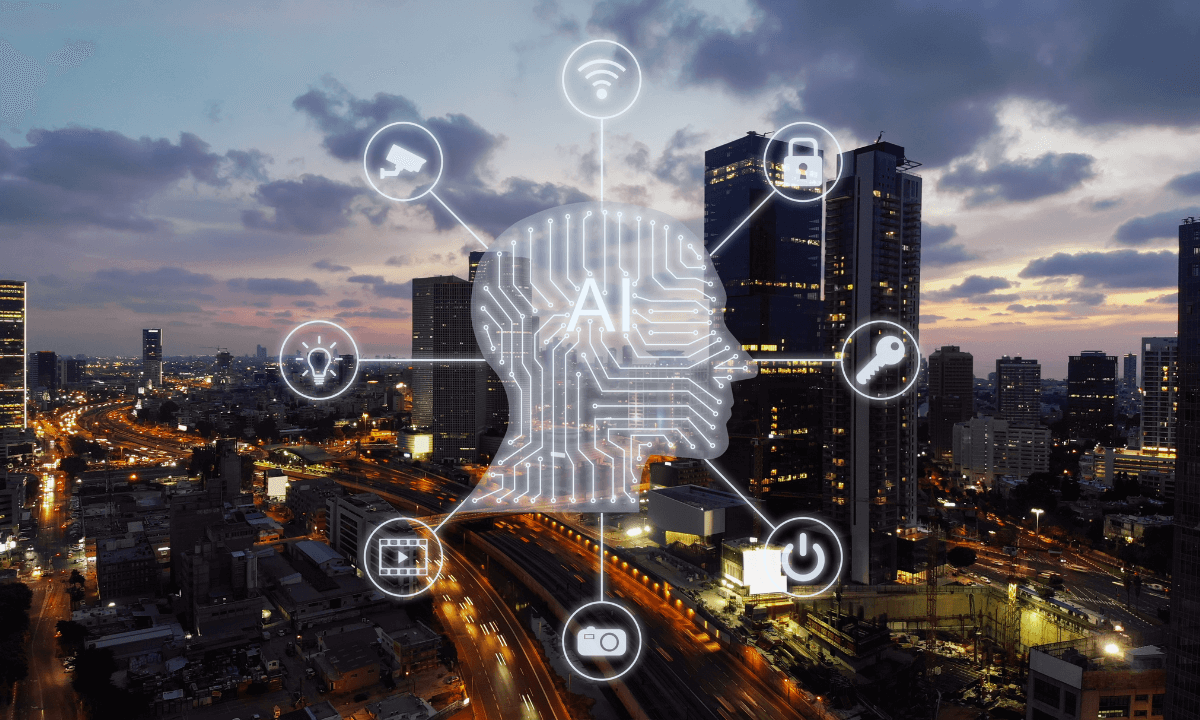
Programmable Logic Controllers (PLCs) have been crucial in transforming industrial automation. Anticipating future advancements, we expect developments that will further transform the landscape of manufacturing and automation.
One notable trend in the evolution of PLCs is the implementation of Artificial Intelligence (AI) and machine learning algorithms. Consequently, PLCs will have the capability to predict maintenance needs, optimize operations, and adapt to changing conditions in real time, ultimately minimizing downtime and increasing productivity.
Moreover, sustainability stands as an increasingly influential trend shaping the trajectory of PLC technology. Future PLCs are anticipated to prioritize energy efficiency and the use of eco-friendly materials, fostering environmentally conscious manufacturing practices. Additionally, PLCs may facilitate advanced analytics for efficient energy management, empowering companies to monitor and reduce their carbon footprint effectively.